o conceptualise a mechanical movement from a blank sheet – almost blank, we should say, as centuries’ worth of pages and equations have already been written on the matter – and to then produce as much of this movement as possible in-house is a long and slow process.
A costly one too, requiring major investments.
When Andi Felsl and Tzuyu Huang embarked on their industrial project at end 2009, they knew exactly what they were getting into. Two years earlier, in 2007, they had founded the Horage brand in Biel. Tzuyu, who is Taiwanese and a graduate of the Berlin School of Economics and Law, was at the head of Momo Plus AG, a major OEM sourcing company (sold to Centres+Métaux Microtech in 2016), supplying components to multiple brands. Andi, from Germany, worked in software and had also developed an innovative suspension system for mountain bikes (a first experience of mechanics).
The brand they created in 2007, as husband and wife, was Horage. Its purpose, as Andi Felsl told Europa Star at Baselworld 2009, was to show that “luxury can be something else, something simple.” The brand was in Basel for the launch of two limited edition watches: a prelude to its first collection, Omnium.
-
- An advertisement for Horage, published by Europa Star in 2009
This was indeed a simple watch. Round, easy to wear, affordable luxury. Every effort had gone into ensuring the quality of the habillage, the rose gold or white gold case in a 35mm or 40mm diameter, the perfectly executed decoration and the quiet sophistication of a facetted sapphire crystal. In line with its affordable luxury ethos, Horage planned to sell direct to customers and, as a “responsible” brand, had committed to donating CHF 1,500 for every watch sold to education programmes around the world. But the movement wasn’t theirs. It was an automatic ETA, modified by Soprod and treated with black PVD.
Build a brand and a manufacture
The brand struggled to get off the ground. There are probably several reasons for this. In 2009 the world was in the middle of a full-on and dangerous financial crisis. Many established brands were suffering. Design-wise, Horage was possibly too far ahead of the curve. Even in this uncertain climate, watches were super-complicated machines for the wrist, the bigger and bolder the better. Horage’s Luxury is not enough slogan had an ambiguous ring.
Andi Felsl would take away something else from this initial experience: “If we were to build a bona fide brand, we had to have our own base movement and we had to manufacture it as independently as possible.” From there, the brand embarked on the creation, from scratch, of its first in-house calibre, the K1. This automatic movement was to be the foundation for future developments.
It would take six years to get there and the help of renowned specialists and movement constructors. The likes of engineer Stephen Kussmaul (ex-Eterna) who worked on the project for three years before handing over to Jonas Nydegger (ex-Eterna) and Florian Serex (ex-Vaucher Manufacture) who in 2015 delivered the K1: an automatic three-hander that was followed shortly after by a version with centre seconds, power reserve and large date.
-
- K1 automatic movement (25.6mm x 4.95mm). The first to be entirely conceptualised, engineered and produced by Horage, it was launched in 2015. Now with silicon lever and escape wheel. Big date, small date, power-reserve indicator (65 hours), small seconds, centre seconds. Unidirectional tungsten rotor. 22 jewels. Accurate to COSC chronometer standard (-4/+6 seconds per day). Designed from the outset as a modular calibre, the K1 is available as multiple configurable variations.
Horage’s adventures in movement land expanded from there. With the benefit of experience and knowledge gained, and by gradually stepping up R&D, the brand developed its second calibre, the K2 with micro-rotor, then a third, the K-TOU tourbillon. It also made a series of improvements and upgrades to the K1 base calibre, releasing numerous variations.
“The K1 movement has a modular design that allows 18 variations with five different complications,” Andi Felsl explains. "With the K2, which is our micro-rotor movement, we increased power reserve to 72 hours and reduced height to 2.9mm, 3.3mm or 3.6mm, with 38 possible variants on this base. All our movements are equipped with silicon escapements and balance springs, are accurate to COSC standard and made from the best materials available.
Currently our calibres are 98% Swiss Made, with 50% of components manufactured at our own or other facilities in Biel and the remaining 48% sourced from suppliers within a 45-kilometre radius." The percentage of components produced directly by Horage is constantly increasing.
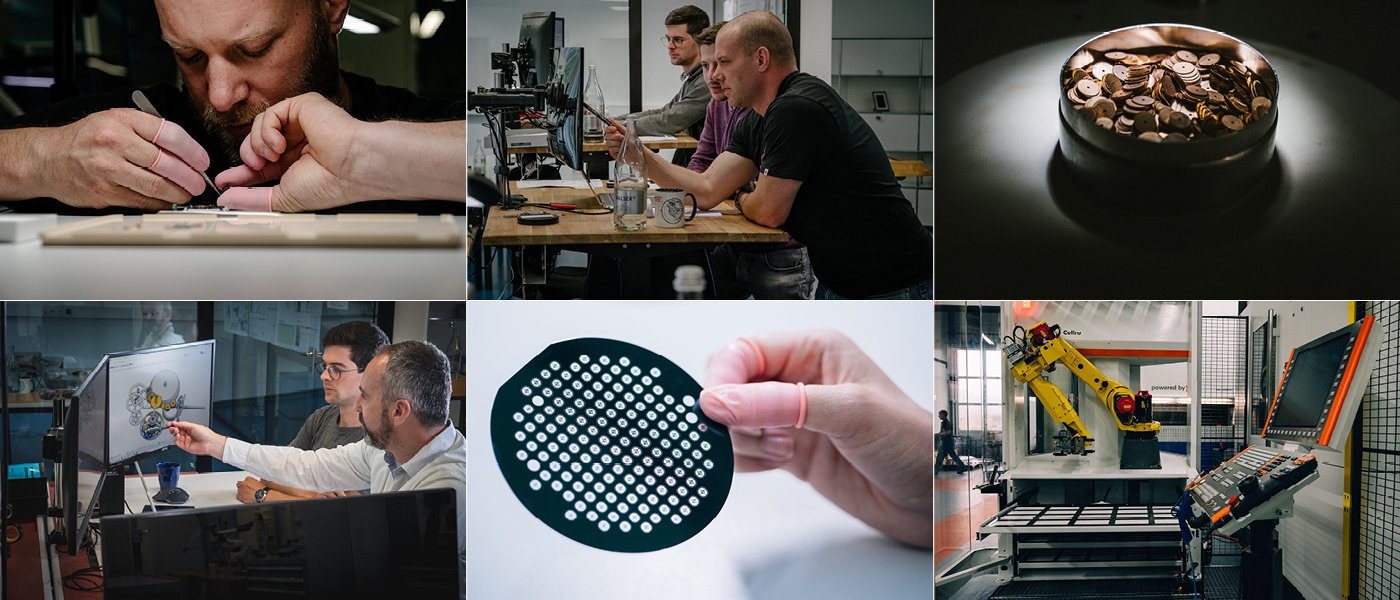
Inside the test site
“We knew it would be a long road and there would be obstacles along the way,” Felsl continues. “Whereas the big brands have a dual structure, with production on one side, brand and marketing on the other, we had to ask ourselves, where do we put the money? Here or there? I truly believe that to become a brand, you have to be capable of producing your own movement. Because we want to exist as a brand, we therefore had to do both at the same time. Build the brand and build the manufacture. Finding the right balance between the two meant we had to design and set up an integrated manufacture that would be as coherent, rational and efficient as possible on a modest scale.”
Andi tells us this as we stand in the middle of the extremely well-equipped “mini manufacture” that Horage has set up in a large space on the outskirts of Biel, which it rents from Paoluzzo AG – an important manufacturer of precision mechanical parts for industry, including watchmaking.
“This is our full-scale test site,” Andi says. “We want to understand, in practical terms, how we can industrialise a manufacture with the least amount of machines, for cutting, milling, rolling, turning, plus laser, engineering and a research laboratory, to produce the volumes we need, which is around 3,000 to 10,000 movements per series. We already have a good level of equipment and can test and launch the first series of virtually every component we need, apart from springs, silicon parts and jewels. We’re in the deployment phase and know precisely which additional machines we need to further increase volume. We have a small, innovative and highly efficient team. Even so, learning how to manufacture isn’t just a question of machines, however expensive. It’s about developing a particular state of mind, a mentality that is geared 100% towards precision, reliability and durability. It’s about balance. Our aim is contemporary industrial production that delivers high quality and precision at the right cost.”
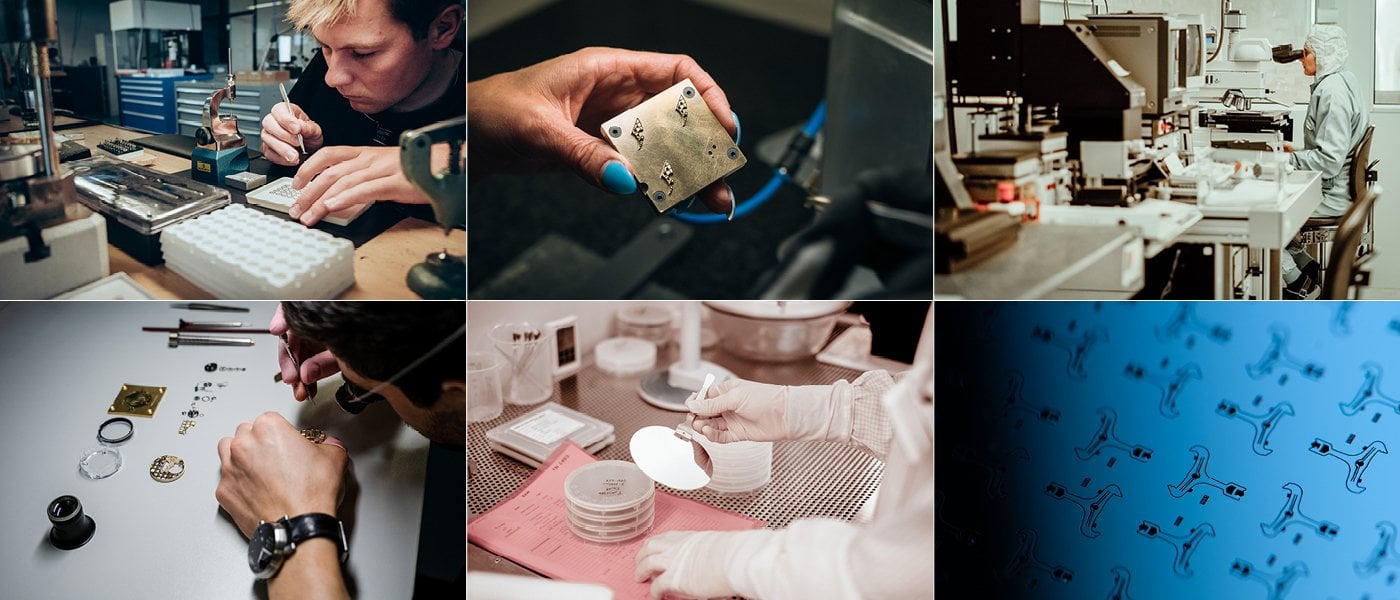
Engineers and watchmakers in one room
A few kilometres away, in a large industrial building in Biel itself, Horage has set up its R&D and design centre, where engineers and creatives work physically alongside the watchmakers in charge of assembling, finishing and decorating the movements. The heads of quality control, sourcing, project management and administration are also based here, making a team of around 25 people in all. All assembly is carried out in-house (which is not often the case). This includes T0 which is the pre-assembly of sub-movement parts such as fitting jewels; an operation that most manufacturers outsource.
Another of Horage’s strong points is its use of silicon. Andi Felsl explains how “the patents on silicon entered the public domain on November 25, 2022 and when they did, we were ready. We immediately sent samples from our first 500 silicon movements for COSC testing. We’ve been working on silicon for the past decade in collaboration with a German company. All our movements are now equipped with a silicon lever, escape wheel and balance spring. We take delivery of the wafers with the different classes [for example between 150 and 500 balance springs per wafer] which we separate and sort. Contrary to common usage, we make our balance wheels based on these classes, so around forty different classes. Manufacturing silicon components isn’t the hard part but managing the process takes competencies that aren’t acquired overnight. But like I said, we’d been preparing for this day for the past ten years.”
“Our objective is to deliver the best quality/performance/price ratio and decoration is part of this equation. Decoration is, by nature, a time-consuming process. Our idea is to obtain a high level of finishing and decoration with the help of technology. In fact I think of us as a tech-mech company. As such, we need to think creatively, combining traditional decorations with more technical designs. You can see this on our K2 micro-rotor calibre.”
-
- As a performance movement that sits between manufacture and industrial counterparts, K2 sports unique decorations. It’s finished with black gold plating and yellow gold lettering, Côtes de Genève on the main bridge, anglage edging and key cutouts that show deeper areas of the movement. The grid pattern is a signature design element and was inspired by the HORAGE logo. Decorations including Côtes de Genève, brushing and anglage are all hand finished. The micro-rotor itself is gold plated tungsten with laser etched tiles resembling the HORAGE logo, and has hand brushed and polished surfaces.
-
- The K2 is a modular movement with 38 possible variants via three different configurations – 2.9mm (Small Second or Centre Three Hands), 3.3mm (Small Second or Centre Three Hands and Calenda) and 3.6mm (True GMT, 12/24 hour day/night Indicator, Power Reserve Indicator, Calendar and Small Seconds or Centre Three Hands). This allows for four integrated complications – power reserve indicator, date, central GMT hand and day/night indicator (with a standard three-hand time setup). The flexibility of this design means that complications can be changed without altering the movement’s dimensions. At only 3.6mm for the movement, Horage’s Supersede comes in at under 10mm in height (9.85mm). Very thin for a loaded sports watch with a water resistance of 200 metres.
And now a tourbillon
Latest in line is the K-TOU flying tourbillon – made possible thanks to experience acquired on the original K1 that was a decade in development. Initially, Horage had planned to buy in tourbillon movements and equip them with its own silicon escapement. Prototypes were made, pre-orders signed, but the deal fell through.
The brand was left with the decision to design and engineer its own tourbillon, with no more than a year in which to do so. Eight months later the K-TOU was ready. All this during the Covid pandemic, an unfortunate period but time out that could be put to good use [Horage is far from being the only company that doubled down on R&D during the pandemic].
The result is a tourbillon with excellent specifications and a unique aesthetic that is also one of the most affordable Swiss Made tourbillons on the market. The Horage Tourbillon 1 launched at a retail price of CHF 7,490.
-
- K-TOU, tourbillon manual winded, has the highest power reserve of the three Horage movements families, with a 120-hour power reserve via a single barrel - a full 5 days. The prior tourbillon prototypes had a 3-day power reserve. Horage’s silicon escapement (escape wheel and anchor) is accordingly 55% more efficient than conventional counterparts, while the flying tourbillon cage is lightweight titanium. Both play a key role in extending the power reserve. The tourbillon cage weighs only 0.29 grams with a low profile of 3.9mm. K-TOU beats at a slightly reduced rate of 3.5Hz (25,200vph), which improves the power reserve as well.
The K-TOU’s design, in particular the grids that structure and protect the movement, give the impression of a robust construction. More than an impression, in fact, as one of the first watches to be equipped with the K-TOU completed a Half Ironman on its owner’s wrist!
As with the K2, architecture and finishing play openly on tradition, represented by the highly polished, almost classical tourbillon cage, contrasting with the industrial aspect of the front and back grids.
Radical choices such as these single out Horage movements and will be even more in evidence on the upcoming K-TMR: a rare combination of a tourbillon and a micro-rotor.
-
- Horage K-TMR
Asked whether Horage plans to sell its movements to third parties, Andi Felsl tells us “we’re first in line but we are open to potential collaborations, should the opportunity arise.”
First, though, Horage is focused on developing its industrial capacity to reach the critical size needed to fulfil its own needs before possibly opening up to future collaborations.