esides setting its sights on the grail of an in-house movement, there is no denying Bremont has an unwavering dedication to re-establishing volume watchmaking on British soil. In its most momentous launch to date, the two-decade-old brand has introduced a new collection featuring its proprietary calibre ENG300 series. The 40mm H1 Generation models feature the first British-made mechanical movements produced at scale for 50 years.
To fully appreciate the significance of this milestone, it requires some background knowledge of the watchmaking industry. Until the 20th century, Britain had been the undisputed horological superpower for over 200 years, as Europa Star previously shared. However, mass production techniques introduced by Swiss and American watchmakers caused a steady decline in the British watchmaking craft, which failed to adapt to changes in the market.
-
- Brothers Giles and Nick English, co-founders of Bremont
Today, a handful of revered horologists such as Roger Smith OBE, Garrick, the Struthers, and the McGonigle brothers keep the light of past glories burning with their fine artisanal watchmaking. Nevertheless, there has been no in-house production at volume since the 1970s when S. Smith & Sons, also known as Smiths for their watches, was forced to close during the ‘quartz crisis’.
Bremont’s 40mm H1 Generation models feature the first British-made mechanical movements produced at scale for 50 years.
Creating a manufacturing base from scratch
In recent times, with no existing infrastructure or a local supply chain, the idea of creating a manufacturing base from scratch had been the stuff of dreams. But that is exactly what Bremont did when, in 2021, it opened “The Wing”, a 35,000 square-foot Manufacturing & Technology Centre in Henley-on-Thames, Oxfordshire. “Being isolated here in the UK, we need to do this ourselves. So having the facility enabled a home [for movement manufacturing] to begin and to deliver on that, and is obviously an essential part of our ambition,” says Managing Director, Chris Reynolds.
-
- Bremont Supernova
Notwithstanding Bremont’s steadfast mission to bring industrial-scale watchmaking back to British shores, Reynolds is pragmatic about the long and arduous journey ahead. “Let’s be clear, for decades now, the Swiss industry has really led the way. It has clearly established standards and quality processes which have to be admired. And we’re starting from a zero position here,” he says, “We began 20 years ago when Nick and Giles had this vision and we’re still on it. We haven’t arrived at the destination yet – we’re still very much on our way.”
Brothers Nick and Giles English formed Bremont in 2002 and launched their first watches five years later. Reynolds joined from the management team of the company’s key shareholder in 2019 to orchestrate the operations. Over time, the company has gradually developed its own horological skillset and in-house engineering expertise. “It’s like a mechanic,” he explains, “Just because you can build or service a Mercedes-Benz doesn’t mean you can go in and work on an Audi. It’s different – the technology is different, the processes are different, the tooling is different – and it’s exactly the same for watches.”
All the while, Bremont has poured big money into The Wing, acquiring new machinery and precision manufacturing know-how. According to Reynolds, the company’s investors have “long-time horizons” of success taking 10, 20, and 30 years to “build a legacy, heritage luxury brand”. “We are investing in the capability – it’s very challenging, very difficult. It requires a lot of time, effort, and dedication. It can be painful at times, I must admit, but we’re persevering.”
According to Managing Director Chris Reynolds, the company’s investors have “long-time horizons” of success taking 10, 20, and 30 years to “build a legacy, heritage luxury brand”.
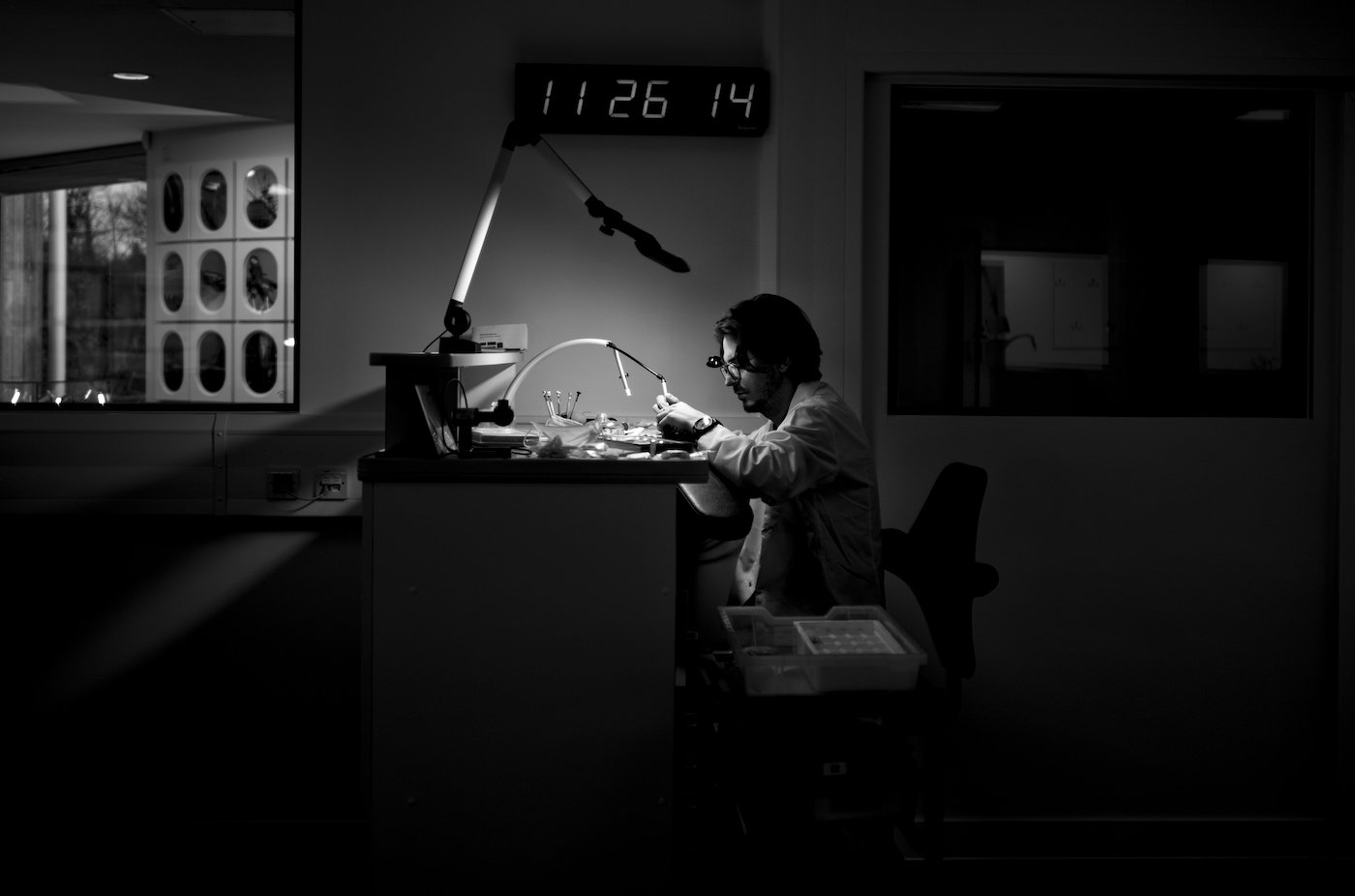
Chasing microns
After years of trials and tribulations, Bremont is decidedly making strides with a blueprint in movement manufacturing. The quest has culminated in the ENG300 series, which takes the K1 calibre base movement by Swiss company THE+ and repurposes it to Bremont’s unique specifications. The team is particularly upfront about this information. It may stem from the blunder of calling its last proprietary BWC/01 calibre an “in-house movement” in 2014 when it was made by a Swiss partner. Cautious about transparency, Reynolds discusses the process of producing the ENG300 on site with no ambiguities.
-
- Bremont Audley
Base components for this new generation of manufactured timepieces are machined on an additional production line at The Wing where there is also a T0-assembly operation. Reynolds shares that the manufacturing centre is now equipped to produce bridges, main plates, other flat CNC machined components such as calendar wheels, date disks, and so on. He stresses, “We’re looking to make thousands [of watches a year in the UK]. We keep hovering around the 10,000-unit mark. It’s been quite consistent now, actually, but the proportion of those which contain our movement is growing and will continue to grow.”
Unlike a small atelier producing limited numbers, making watches en masse is a complex process requiring in-depth analysis and vigorous testing at every level prior to execution. “One of the things that is possibly the most difficult to comprehend is the sheer scale and volume of sub-assemblies that go into a movement assembly,” Reynolds explains. “There are countless numbers of sub-sub-assemblies where you’re pressing together gears or wheels or bearings with spring-loaded kind of pinions. These are tiny, tiny parts. Their alignment, the tension, and not damaging the parts when you’re doing it are crucial. And if you’re slightly out in any way, it will result in a watch which does not keep good time. So, we’re chasing the microns through the movement to result in nanoseconds of accuracy.”
The quest has culminated in the ENG300 series, which takes the K1 calibre base movement by Swiss company THE+ and repurposes it to Bremont’s unique specifications.
Making movements for other watch brands?
Bremont goes to great lengths to pursue industrial-level reliability. All ENG300-powered watches undergo Bremont’s own ISO-standard testing, which is directly comparable to the ISO3159:2009 chronometer test, and equivalent to COSC, the official Swiss chronometer test. “We are doing that in-house,” says Reynolds, “Unfortunately, there is no suitable independent body where we can get our movements tested to the standard we demand so we do it ourselves.”
Bremont then goes one step further, testing its movements with the rotor, the date disc, the complications, and all the sub-systems fitted. “It gives us control,” adds Reynolds. “We’re able to test the movement in its entirety without having to remove any parts. It ensures the quality, and the standards are actually higher than what you’d see if you were to ship them externally. On top of that, it reduces the risk of damage or any kind of deterioration to the performance.”
-
- Bremont Fury
In a nod to Britain’s illustrious horological past, Bremont named this rigorous testing process the H1 Timing Standard, after legendary clockmaker John Harrison whose first H1 marine timekeeper helped solve the problem of finding longitude at sea. But the historical references don’t stop there. The H1 Test also aspires to the old Kew Test – a stringent chronometer testing process developed in the 18th century at the preeminent Kew Observatory in London.
Watches with a “Class A” Certificate from Kew were deemed the gold standard in precision timekeeping. Bremont clearly wants its products to be held to a higher standard and sees this as a sound business decision to differentiate the H1 Generation. But for Reynolds it also means another step towards rebuilding Britain’s lost industry. “I would be very happy to find ourselves in a position in the future where we have surplus capacity to make movements for other watch brands and engage them on an independent testing standard as well. So, we’re playing a part, and hopefully bringing all that back.”
Like its famous horological forefathers, Bremont is dreaming big. It also wants to bring its customers and the wider community onboard for the ride. Reynolds offers a final ambitious thought for the future: “Wouldn’t it be great if there were British companies supplying back into Switzerland because we were better at it? That would be so cool.” A dream is only a dream until it becomes a reality.
In a nod to Britain’s illustrious horological past, Bremont named its testing process the H1 Timing Standard, after legendary clockmaker John Harrison’s H1 marine timekeeper.
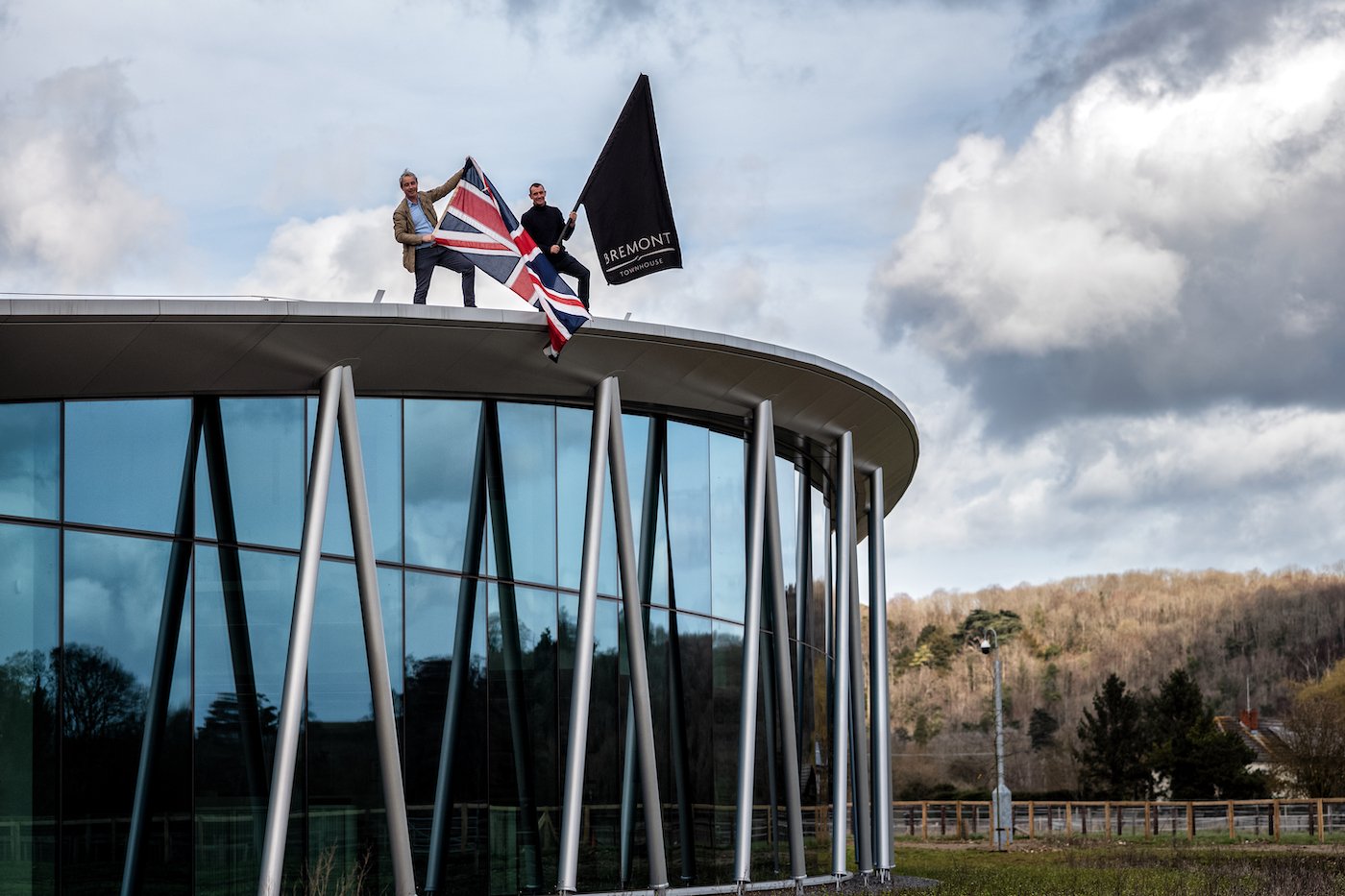