n the far side of the watchmaking town of Le Locle, just beside the underground mills of the Col-des-Roches is a building where exceptional materials are produced. Comadur (a contraction of the French for “Components from Hard Materials”) specialises in producing components of proven hardness, requiring particularly demanding treatments: synthetic crystals (sapphire, rubies), ceramics and micro-components. This Swatch Group entity is one of the well-kept secrets that enable the Swiss watchmaking industry to continue to innovate in materials research.
One of its main clients within the group is Rado, whose slogan is “Master of Materials”. This champion of high-tech ceramics, which were introduced as early as 1986 in its Integral model (thanks to a collaboration with Comadur), produces watches whose texture is reminiscent of a second skin: silky, ultra-light and scratchproof, it adapts to body temperature.
-
- Ceramics has been the focus of Rado for many decades, as our own archives show (a document from 1991).
- ©Europa Star Archives
But manufacturing high-tech ceramic is far from easy, involving meticulous processing of the basic powders and absolute mastery of the heating temperatures of what is a very tricky material to work with. The roots of Comadur, which employs more than a thousand people at seven production sites across Switzerland, go back to the consolidation of the watch industry following the quartz crisis: the company was created in 1984 by the merger of Seitz & Co, Méroz Pierres SA, Sadem SA and Watch Stones & Co SA, which were themselves the result of various successive mergers. The oldest among them, Méroz Pierres SA, began manufacturing watch jewels in 1880.
This Swatch Group entity is one of the well-kept secrets that enable the Swiss watchmaking industry to continue to innovate in materials research.
An unusual type of ceramic
For the several million ceramic pieces (mainly cases, dials, bezels and bracelets) that Comadur manufactures each year, everything starts with a chemical process. The company calibrates its own primary materials – in this case zirconium oxide (ZrO2), in powder form. “The broadest and most basic definition of ceramics is a non-organic, non-metallic chemical compound that hardens on firing,” says Oian Nicolas, CEO of Comadur. “It is very much a part of everyday life, from tiles to pottery. However, our approach to this process is high-tech: we use extremely pure and fine synthetic zirconia powder to design a very dense, non-porous material – unlike your pottery which is not 100% waterproof.”
Two main manufacturing processes are used: pressing, where the powder is compressed; and injection moulding, the most common method used in the production of Rado ceramics. This technique makes it possible to create more complex shapes. Zirconium oxide is supplemented by pigments that are resistant to very high temperatures, to colour the ceramic, as well as polymers (patented by Comadur) to help with the injection moulding process. “The manufacturing process of our ceramics is very delicate because no contamination, however small, can be tolerated,” explains Oian Nicolas. “For example, a trace of iron will make the material come out yellowish.”
-
- Injection moulding
The first step in the process is to define how the piece can be manufactured to fulfil the design brief drawn up by the brand. There is one major constraint: during the firing process, the piece shrinks by approximately 25% due to the effect of temperature – something that must be taken into account when designing the injection moulds. Simulation software is used to test how the materials will react, in order to create the most accurate mould possible.
-
- Laser engraving
Once moulded, the parts are placed inside an oven and exposed to an extremely high temperature (1,450°C) for several hours. This sintering process hardens the ceramic and transforms it into its final colour, while at the same time the polymer evaporates. The component is then machined to its exact dimensions, using diamond tools. This is followed by polishing, immersing it in a bath containing high-frequency vibrating ceramic fragments; sandblasting, which creates a matt finish; laser engraving of any inscriptions (such as the numbers on the bezel), which are then lacquered; and finally, quality control.
There is one major constraint: during the firing process, the piece shrinks by approximately 25% due to the effect of temperature – something that must be taken into account when designing the injection moulds.
Contemporary alchemists
Thanks to the work of Comadur, Rado was also able to introduce new coloured ceramics in 2019, in the True Thinline Les CouleursTM Le Corbusier models, ranging from an intense bright orange to a delicate pale sienna. Various oxides are mixed with the base powder to obtain the desired colours, a subtle work of contemporary alchemy. “In ceramics, black is the simplest colour to produce, paradoxically much more so than white, even though the chemical compounds appear white at the beginning of the process,” says Oian Nicolas.
-
- Rado Captain Cook Chronograph
Rado also introduced an extraordinary new finish, thanks to an effect first discovered accidentally more than two decades ago: plasma, which gives the ceramic a metallic appearance. This effect is particularly appreciated at a time when the watch industry is dominated by sport-chic models in steel. Comadur is one of very few entities in the world to master this technology, which sees the zirconium oxide pass under a plasma torch that can reach 20,000°C (protect your eyes when visiting!), stripping away the oxygen atoms. The addition of carbon results in the formation of zirconium carbide - another ceramic - which has an appearance close to that of steel, while retaining the advantages of ceramics: scratch-proof, light, silky, hypoallergenic, durable (as opposed to a PVD coating, for example). And without any metal.
-
- Comadur is one of very few entities in the world to master plasma technology, which sees the zirconium oxide pass under a plasma torch that can reach 20,000°C (protect your eyes when visiting!), stripping away the oxygen atoms.
Under the impetus of Rado, Comadur has also developed other ceramics such as CeramosTM, a material composed of 90% high-tech ceramic and 10% metal alloy. In addition, it has developed ultra-light high-tech ceramics using silicon nitride. Over time, the company has also experimented with different decoration techniques on its ceramics, which can be found throughout the different Swatch Group brands: gold, varnish, Liquidmetal, Super-LumiNova®, inlay of precious stones, etc.
Rado also introduced an extraordinary new finish, thanks to an effect first discovered accidentally more than two decades ago: plasma, which gives the ceramic a metallic appearance.
Several million sapphire components
Comadur’s other major speciality is synthetic sapphire. Several million pieces leave its various sites each year: most of them are watch crystals, but the company also makes dials and bezels. Here, the basic ingredient is aluminium oxide. A flame heated to 2,050°C melts the alumina powder and, as the molten droplets solidify, a single cylindrical crystal forms, just like a stalagmite. The result of this operation, known as the “Verneuil method”, is a synthetic sapphire monocrystal, which is then stabilised before being cut with a diamond wire to obtain the sapphire glasses that are used to protect watch dials. At its Bad Zurzach site, Comadur has no fewer than 550 torches dedicated to this industrial operation!
Another method of producing synthetic sapphire, which has the benefit of avoiding any loss of material during manufacture, is known as “EFG” (edge-defined film-fed growth). It is used in particular for crystals that require specific geometries, dimensions and thicknesses. A metal crucible, usually made of tungsten or molybdenum, contains a bath of molten alumina from which the sapphire crystal is generated. A seed is dipped into the surface of the bath, causing local solidification due to the temperature difference between the seed and the bath. The crystal is then formed by the action of an upward movement, allowing the material to solidify as it rises.
-
- Rado Captain Cook High-Tech Ceramic
Comadur produces single sapphire crystals in the form of slabs up to 1.5 metres long, 15 cm wide and several millimetres thick. Implemented in 2017, this method has made it possible to recycle several years’ worth of unused sapphire material. Thus, the waste from one process becomes the raw material of another. This recycling of raw material is in line with the sustainability approach taken by Comadur and the Swatch Group.
Very few coloured sapphires are produced – with the notable exception of rubies, which belong to the same family. CNC machines and specific tooling have been developed with external suppliers to handle this complex process. Between 40 and 70 separate operations are required to produce the crystal that protects the watch dial. Various different finishes are available: anti-reflective, ghost effect, touch-sensitive (for the T-Touch), etc. Comadur produces more than 100 tonnes of sapphire per year using the Verneuil process and 25 tonnes using the EFG process.
Implemented in 2017, the EFG method has made it possible to recycle several years’ worth of unused sapphire material. Thus, the waste from one process becomes the raw material of another.
Where energy meets matter
From Le Locle, we then travel the 60 kilometres that separate Comadur from Rado’s headquarters, just outside Biel. There we meet Adrian Bosshard, a former Swiss motorbike champion and a longstanding presence in the Swatch Group. After 17 years at the helm of Certina he took over as head of Rado in 2020. After observing the production of the ceramics that equip the majority of the brand’s watches, it’s easy to understand why Rado has built up “a very loyal community of customers”, as Adrian Bosshard points out. The sensation on the wrist is so unique that it will leave no one indifferent: some may not want to wear anything else...
-
- After 17 years at the helm of Certina, Adrian Bosshard took over as head of Rado in 2020.
For the man in charge, the Captain Cook High-Tech Ceramic launched last year perhaps best represents Rado’s success, in an era fascinated by historical models. It’s a combination of a design dating back exactly sixty years, which takes the fashionable codes of the dive watch, and a material that is the result of the cutting-edge technology mastered by the engineers of Le Locle, producing a refined and highly contemporary feel. The advantage of ceramic is that it does not age, even if the design it embodies is itself vintage. It is also a material so unique that it cannot really be put in any category, which is good news in an age that has turned its back on classification.
-
- Introduced this year, the Captain Cook High-Tech Ceramic Diver is the result of Rado’s latest high-tech ceramic production techniques. It is available in six different variations (including two Plasma versions).
This spring, Rado launched a new ISO-certified Captain Cook Diver and equipped its 1962 flagship watch with a chronograph. In this anniversary year for the collection, the brand also unveiled a limited edition, the Captain Cook Over-Pole, a 37 mm timepiece with distinctive vintage codes. A strategic launch in the second half of the year was the relaunch of the Diastar Original, the pioneering scratchproof watch, particularly recognisable thanks to its shaped case. Born in the same year as the Captain Cook and a key Rado model, the Diastar Original has been produced and sold continuously by the brand for the past 60 years, representing a total of more than five million pieces over the decades.
-
- In 1962, Rado unveiled a pioneering scratchproof watch: 60 years later, the DiaStar Original gets a makeover. An article from 1962 in Europa Star.
- ©Europa Star Archives
Innovation will remain crucial if Rado is to defend its title of “Master of Materials” over the longer term: “I come from the world of sports competition and I have learned that even if you break a record, another racer will eventually catch up with you,” says Adrian Bosshard. “There is always room to grow: plasma and coloured ceramics demonstrate this, as does the magnetic field-resistant Nivachron that equips our movements.”
“There is always room to grow: plasma and coloured ceramics demonstrate this, as does the magnetic field-resistant Nivachron that equips our movements.”
-
- Launched in 1962, Rado’s iconic DiaStar Original is being reborn on the occasion of its 60th anniversary. A special edition has been created by designer Alfredo Häberli, framed by a radial-brushed Ceramos coiffe with polished angles. The Rado R764 automatic movement guarantees a power reserve of 80 hours.
Ceramics remain Rado’s particular playground. Other brands have adopted the material, but not to the same extent. This well-defined strategy also means that the watchmaker is departing somewhat from the sector’s traditional supply channels and has better control over its production. Provided, of course, that it can secure its supply of basic materials, at a time when other brands are building up their stocks of gold and steel ahead of what will be a difficult winter for any facilities relying on very high temperature ovens. Where energy meets matter: this is an apt way of describing the process that results in the creation of Rado’s highly individual watches.
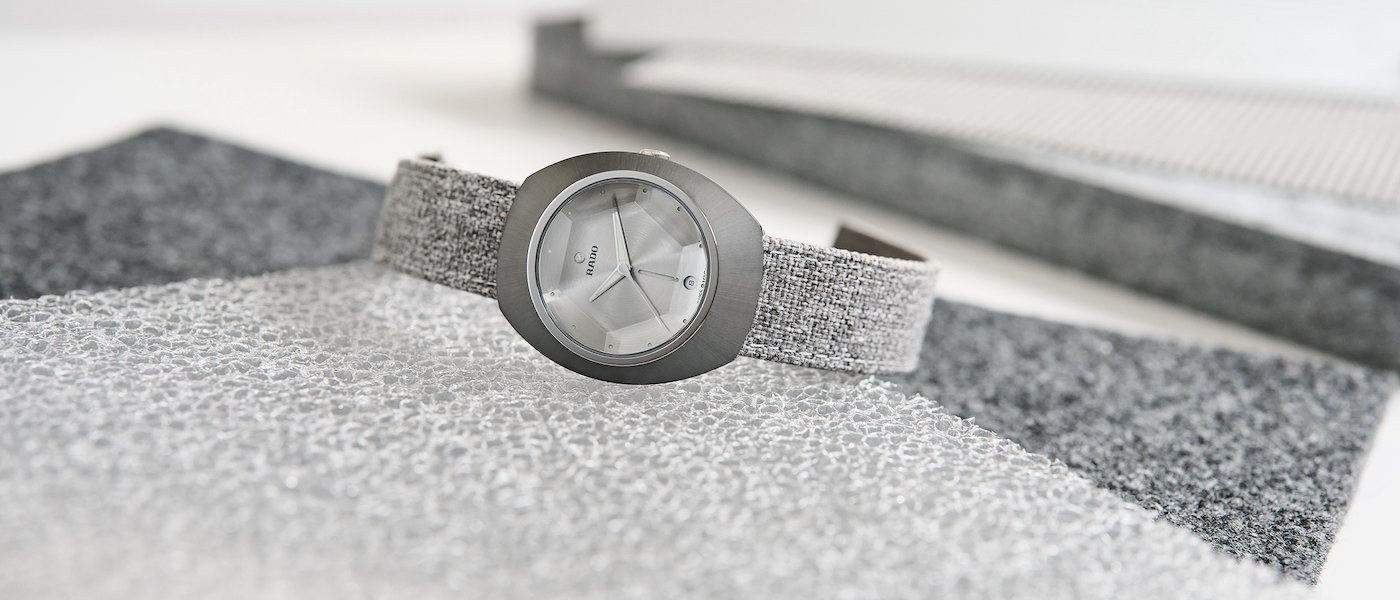
THE STAGES OF CERAMIC PRODUCTION
-
- MOULD DESIGN - A mould is created from sketches by the brand’s designer.
-
- INJECTION MOULDING - The mould is placed deep inside the huge machine where the injection process takes place.
-
- SINTERING - The cases are placed inside a special kiln, fired to an extremely high temperature (1450°C). Over many hours the ceramic fully hardens and acquires its intense final colour and maximum hardness, while the polymer evaporates. During this process, the case shrinks by about 25% to its final size.
-
- MACHINING - The final precise dimensions are machined with diamond tools to achieve the necessary accuracy.
-
- POLISHING - Components destined for exceptional shine are plunged into a bath of tiny ceramic fragments vibrating at high frequency.
-
- SANDBLASTING - Precision sandblasting is used to produce a matt finish with uniform smoothness.
-
- ENGRAVING - A laser etches numbers and markings onto the bezel, creating perfect outlines and depressions.
-
- PLASMA KILN - Components destined for high-tech ceramic plasma finishing undergo a further firing in the kiln. The initial white colour is transformed into a permanent metallic shade and finish.
-
- LAQUERING - The tiny voids made by the laser are filled with a lacquer that bonds permanently to the ceramic once it’s dry. This delicate, dextrous work is done by watchmakers.
-
- QUALITY CONTROL - A rigorous inspection is performed to ensure the final result meets the brand’s standards.