rom the bay window we can count dozens of assembly lines, ranging from 50 metres to 150 metres long. We were certainly expecting this when we visited the Miyota factory, opened only three years ago. But what is particularly striking at first sight is the very limited number of employees working on the lines, all equipped with safety masks that make them blend into this industrial landscape. “One or two operators are enough to manage a production line,” we are told.
What is really striking at first sight is the very limited number of employees who work on the lines.
-
- One or two operators are enough to manage a 50-metre-long assembly line in this Miyota factory.
The only operation that is still done by humans here is moving components from one hall to another. But not for long: automation of transfers between the four production rooms is in progress, via conveyor belts.
One movement per second
The Citizen Group’s movement brand, which was launched in 1959, now produces some 100 million calibres per year in its various factories. Most of them are quartz calibres. Saku, in Nagano province, is the group’s largest facility.
-
- An aerial view of Miyota’s movement assembly factory in Saku, Nagano province.
This circular building with a surface area of 83,000 m2 was opened in 2016. It operates with not much more than 200 employees working in shifts, and its production rate is one movement... every second. Miyota supplies both third parties and the Citizen brand. Unlike ETA, it has not implemented any restrictions on deliveries, even to brands that may compete with Citizen.
Everything is done internally
Miyota’s production capacity, the result of ever-increasing automation, allows it to remain competitive, even though world demand for quartz calibres is falling and Chinese competition is fierce. The company’s cash cows are the 2035 and the Super 2035.
Even the oil used in the machines is a “homemade” product.
In Saku, components from all over Japan are assembled on some 55 highspeed lines. The Citizen Group is highly integrated, since it is also a major player in the manufacture of machine tools and CNCs, which it supplies internationally. Even the oil used in the machines is a “homemade” product.
The latest innovation is the digital detection of problems and defects on assembly lines: at regular intervals, an alarm sounds and components are discarded down a separate track. And there’s another step towards automation on the horizon; in the factory, the latest buzzword is Internet of Things.
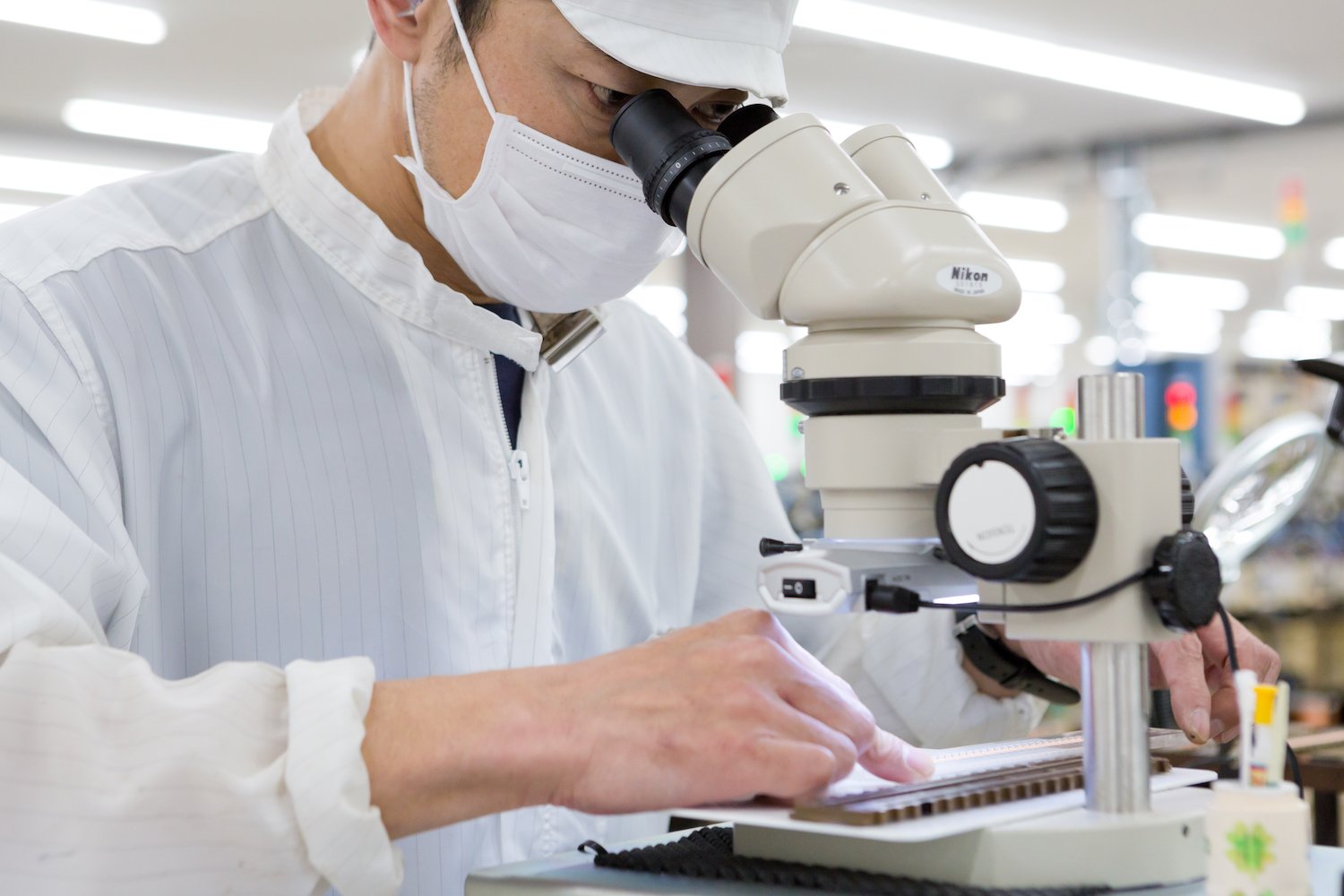
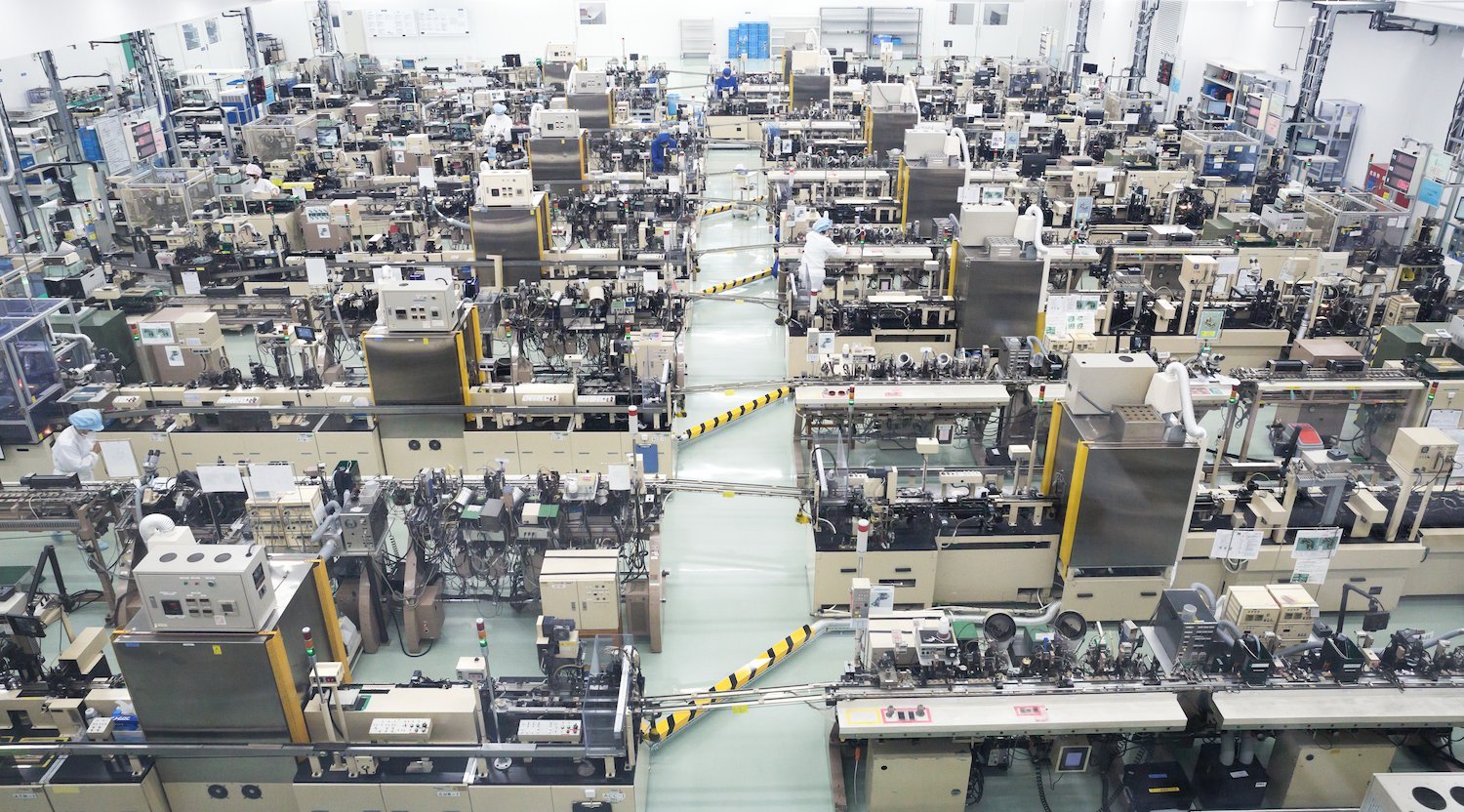
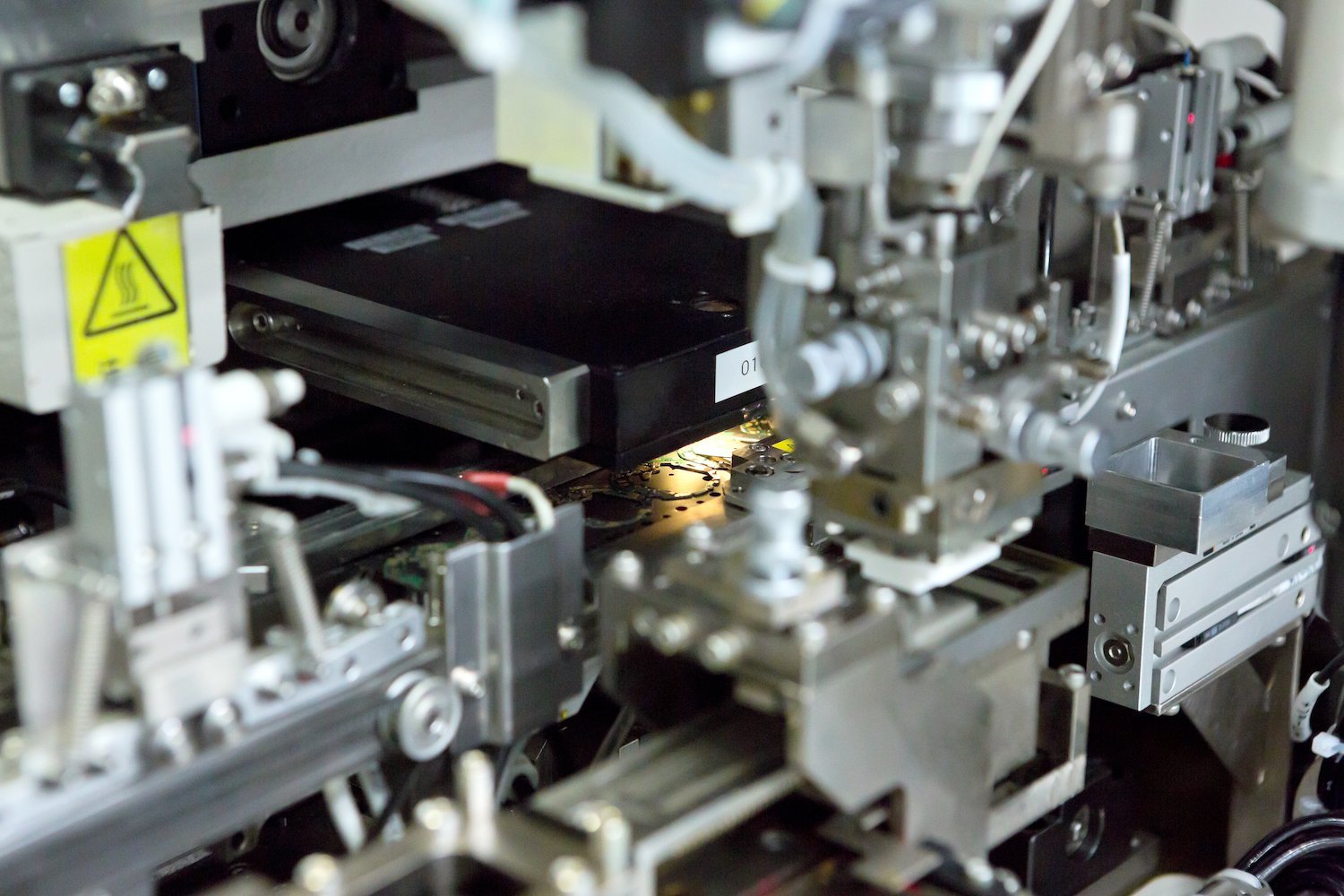
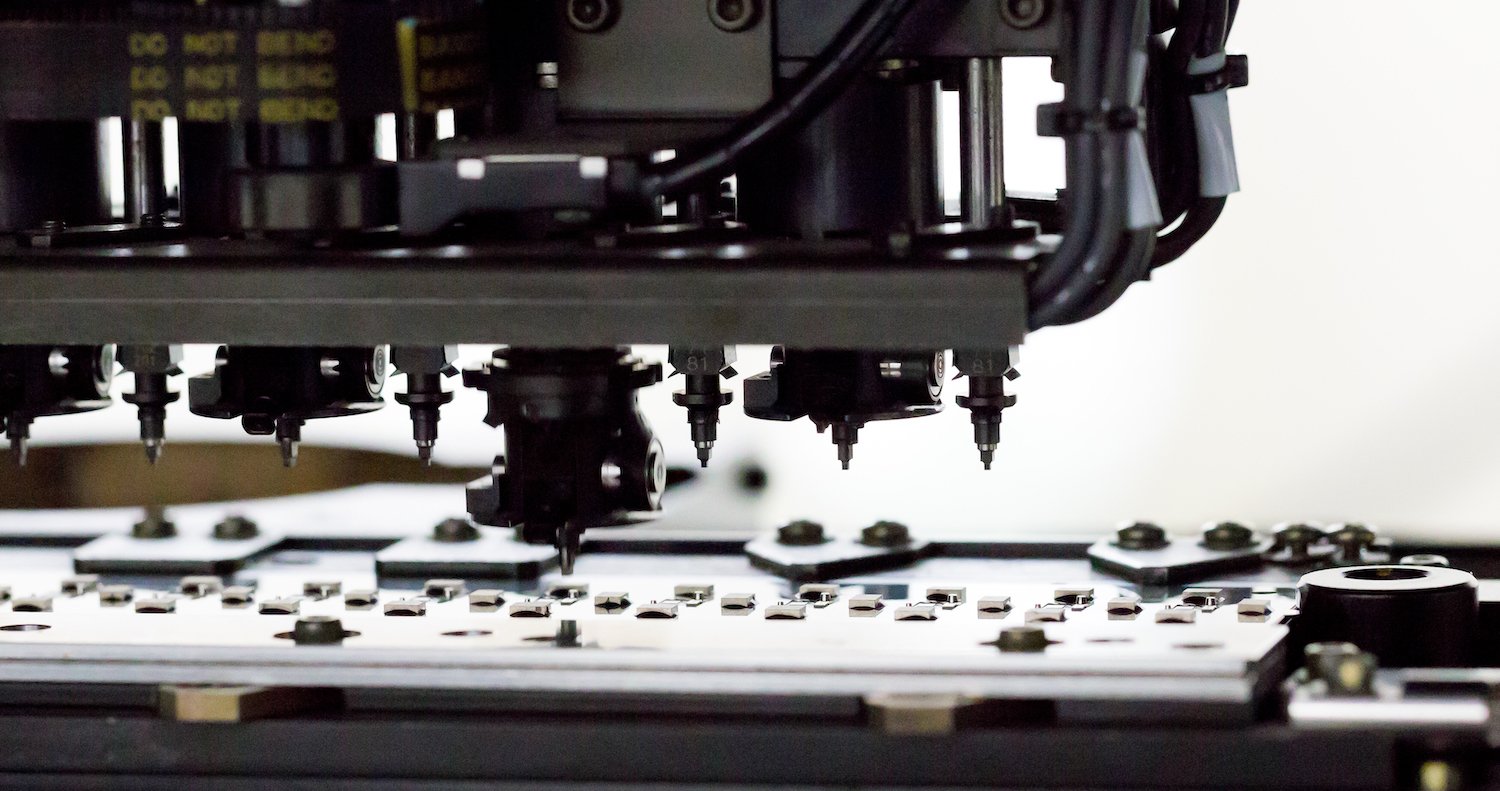
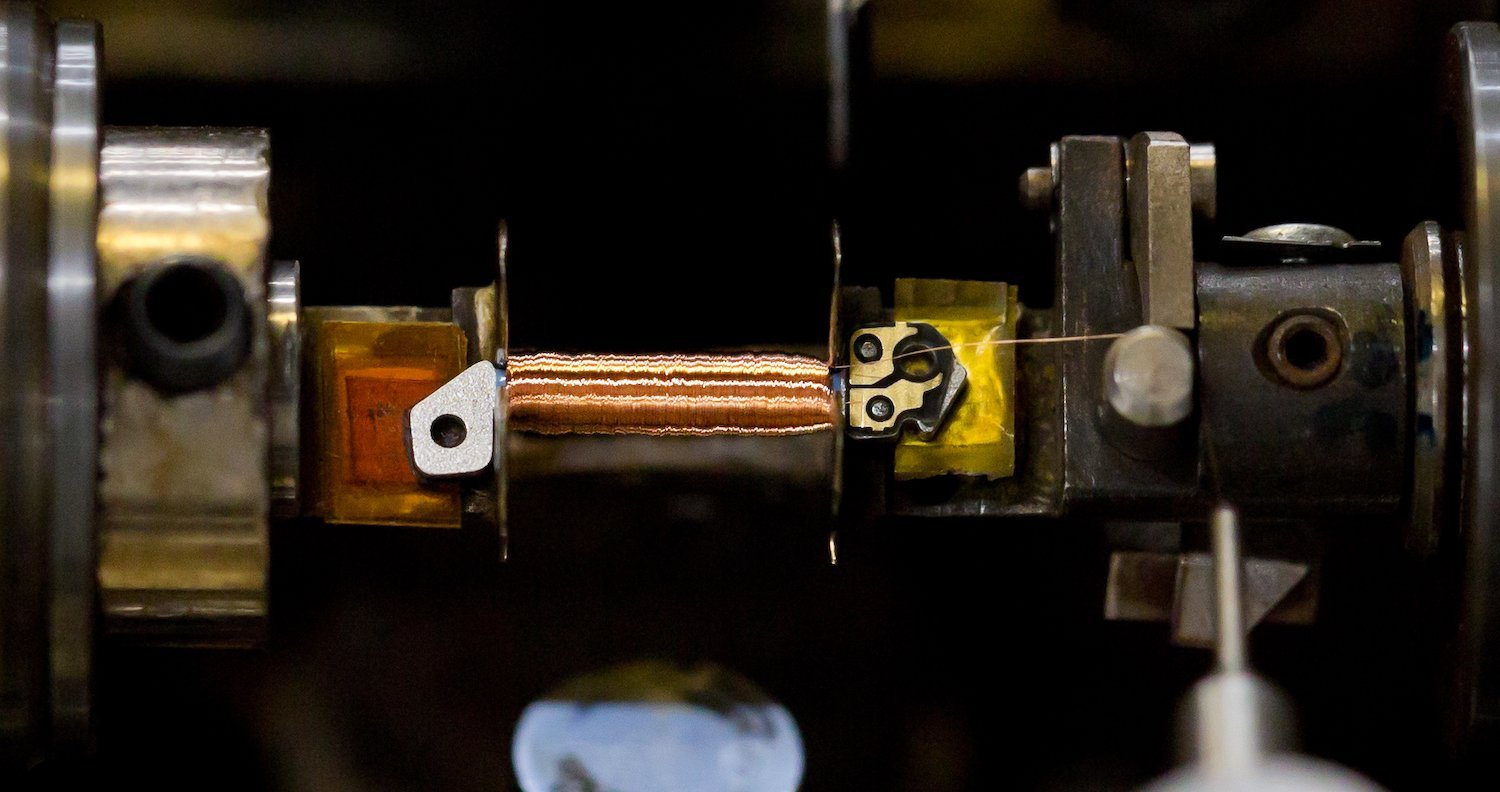
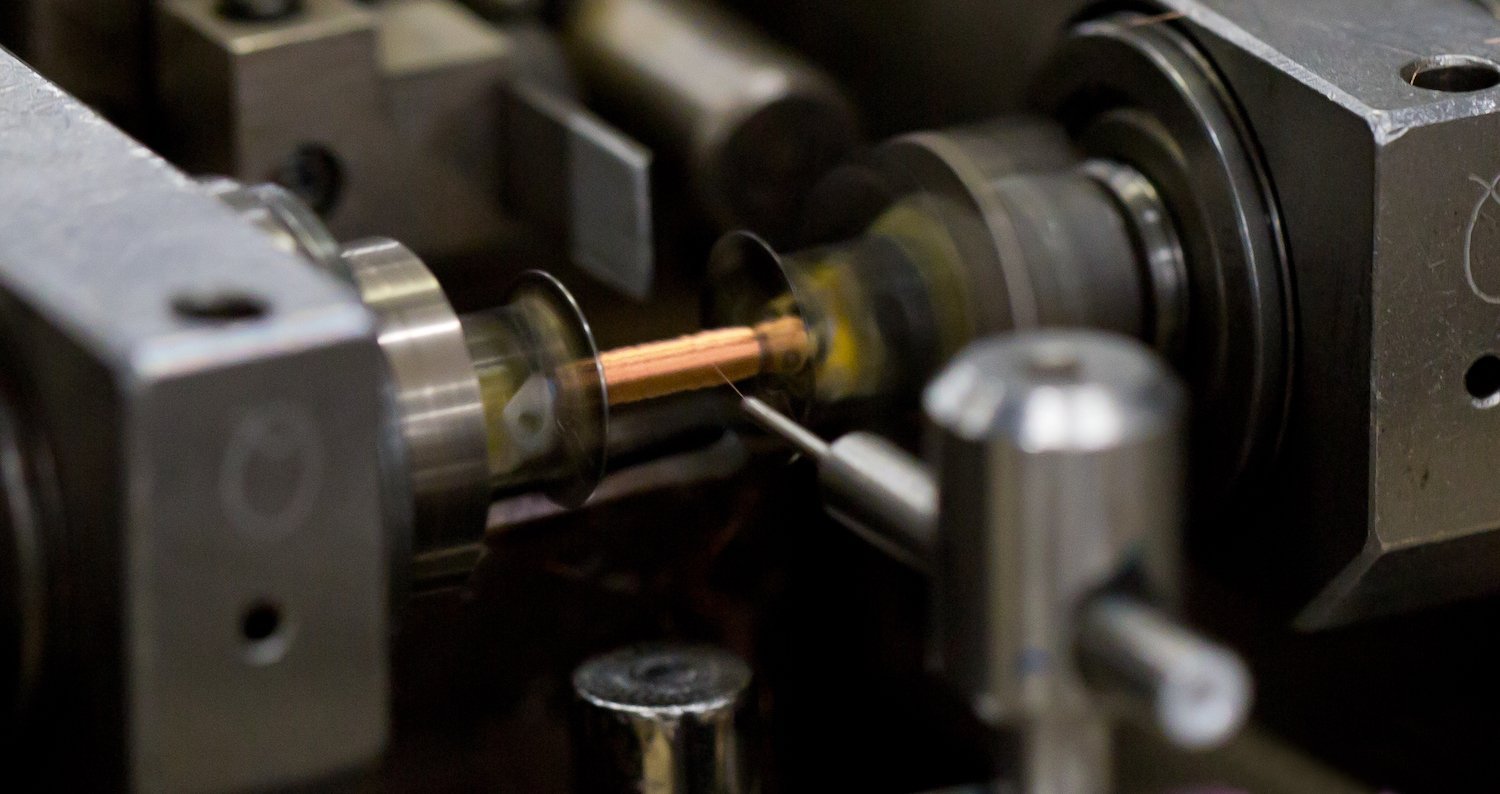
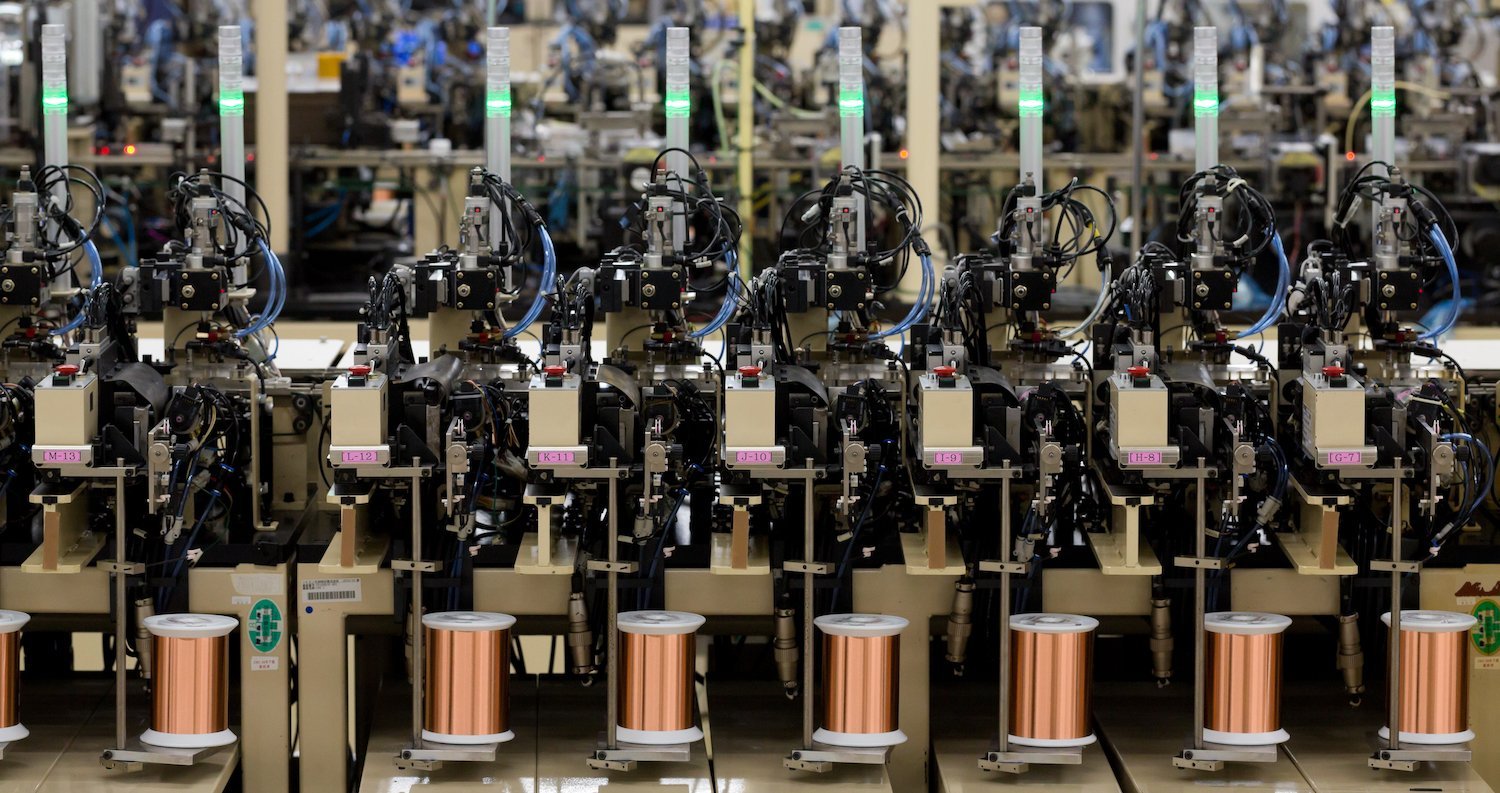
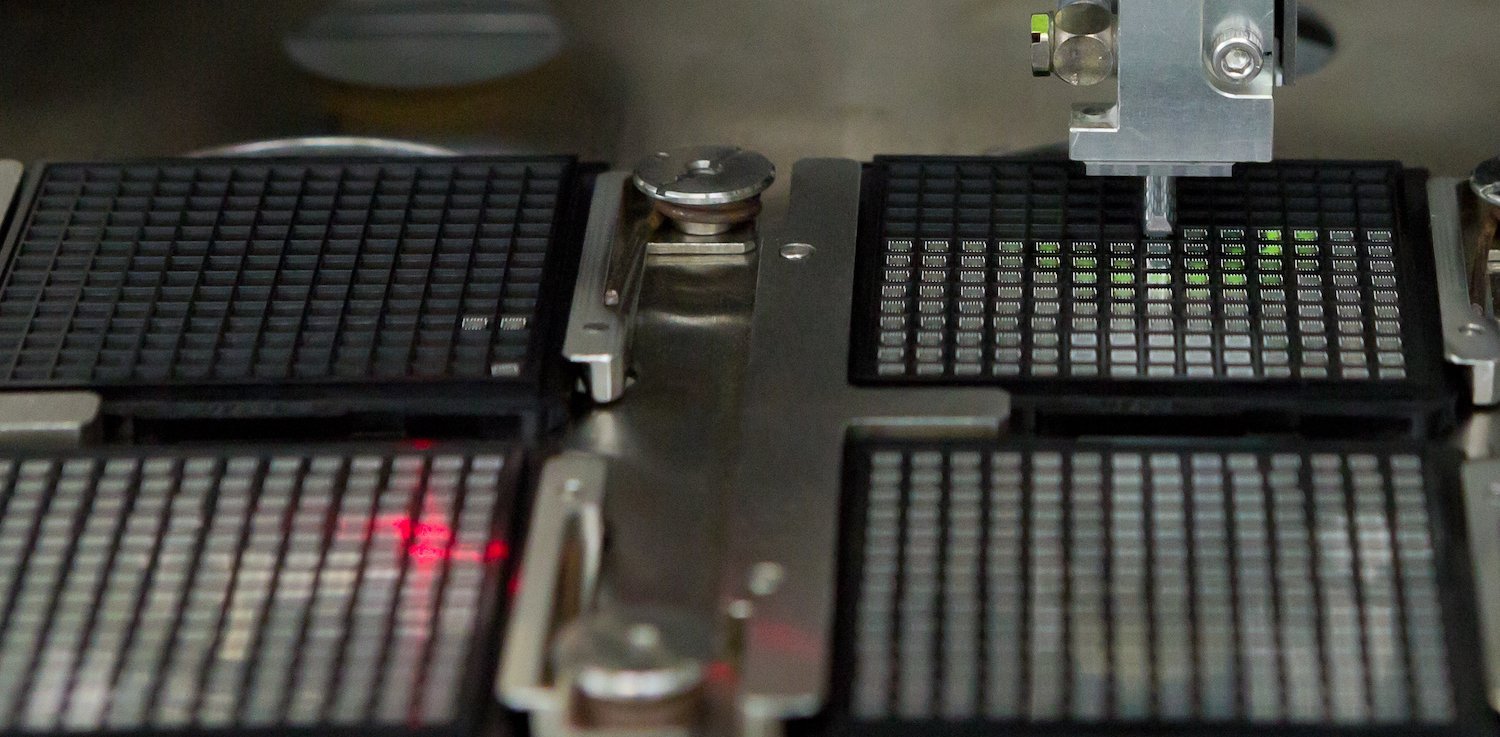
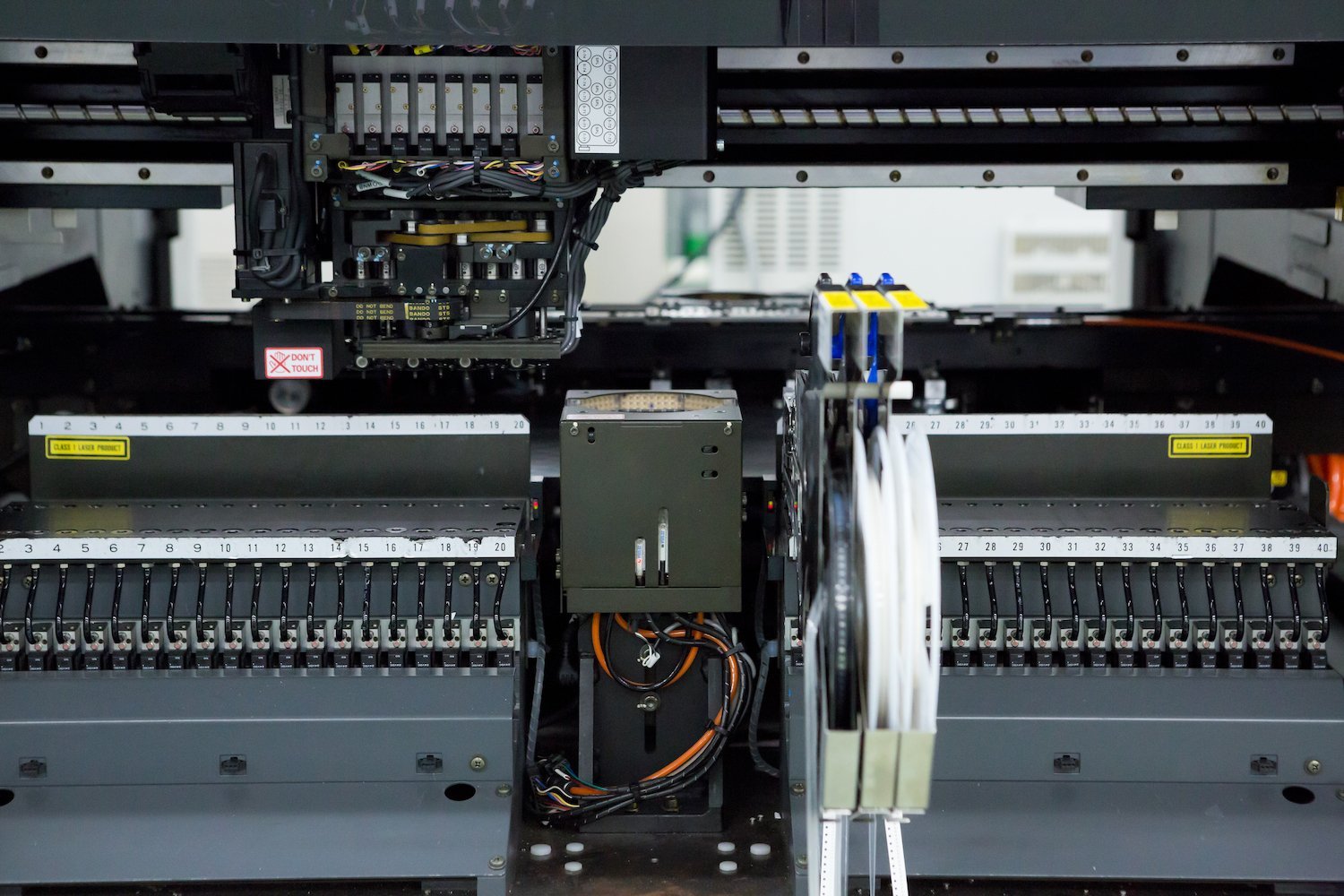
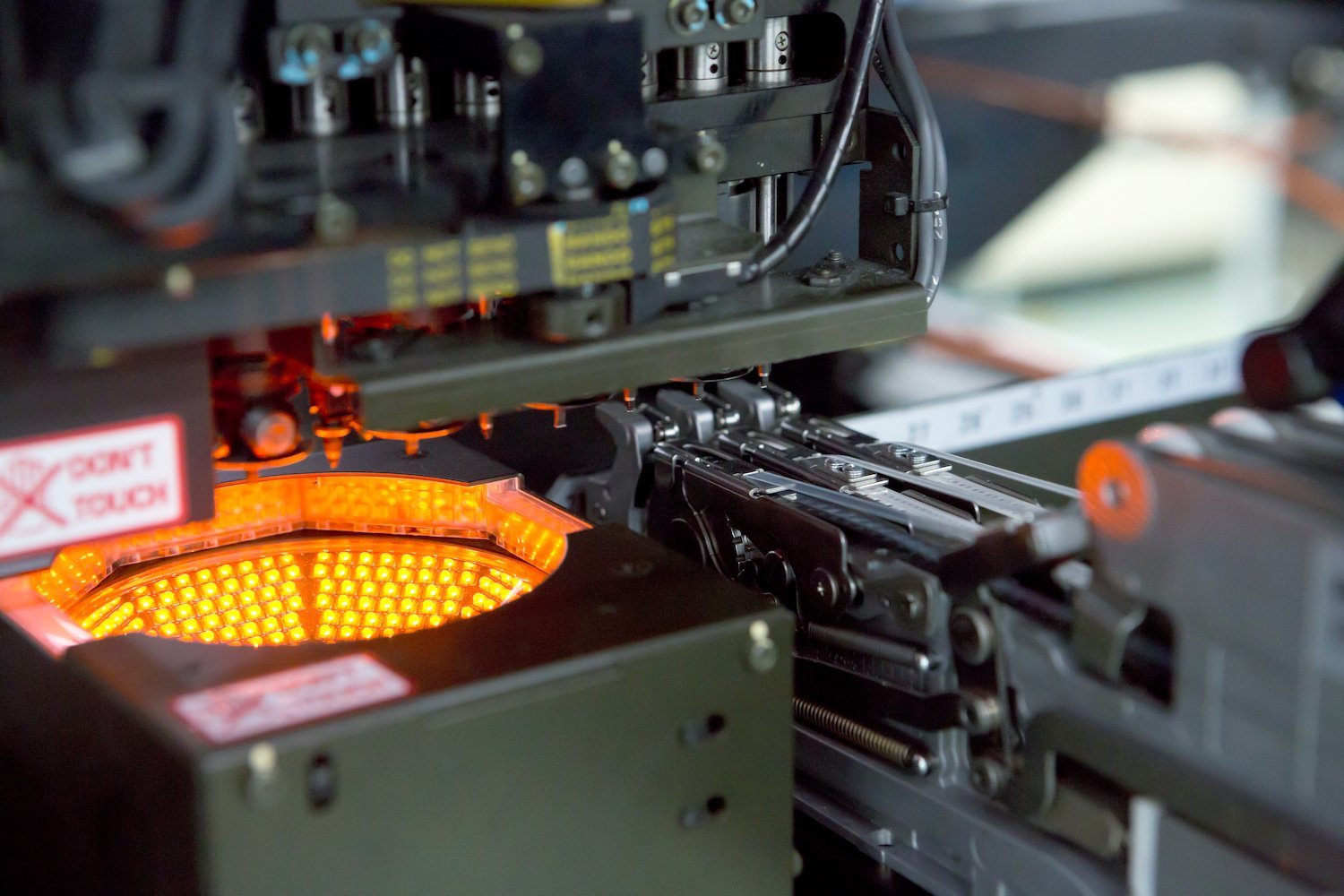