ome of the world’s largest gold refineries are located in Switzerland: Metalor in Neuchâtel (NE); Cendres + Métaux in Biel/Bienne (BE); Pamp in Castel San Pietro (TI); Valcambi in Balerna (TI); and Argor Heraeus in Mendrisio (TI). Some 70% of the world’s gold is processed in Switzerland, according to various sources.
One of these companies is located at the heart of the watchmaking ecosystem, in Marin in the canton of Neuchâtel. A visit to the Metalor factory gives an idea of the extent of the challenges facing this industrial group, one of the world’s largest gold smelters. The issues are numerous: traceability and social impact of supply, electricity consumption in production, transport of materials, and use of chemicals. How does Metalor manage these challenges? And what are the consequences of the choices it has already made?
One of these companies is located at the heart of the watchmaking ecosystem: a visit to the Metalor factory gives an idea of the extent of the challenges facing this industrial group.
The complexity of managing multiple certifications
Antoine de Montmollin, Metalor’s CEO, insists that his company does not rely solely on the standards established by existing certifications, which are so numerous that they can become impossible to understand. “We actually have only one standard: our own. We go beyond local legislation through our group standards. Some countries, such as Russia, are even excluded from the lists of potential customers. Our partners have to meet our requirements and we organise regular on-site compliance visits to ensure that our standards are met – for gold and for all other precious metals.”
Metalor was the first refiner to be granted Code of Conduct and Code of Practice certification by the Responsible Jewellery Council (an organisation now in turmoil as a result of the Russia-Ukraine conflict – read our article on this subject). It is also one of the founding members of the Swiss Better Gold Association, launched in 2013, and the first in the industry to be accredited as a referee by the London Bullion Market Association (LBMA) and the London Platinum and Palladium Market (LPPM). The company nevertheless continues to collect certifications – it has 29 to date!
-
- The Metalor ecosystem
This high number of certifications requires continuous monitoring. “An entire department is dedicated to this activity and we carry out audits all year round,” explains Antoine de Montmollin. “This is the cost of guaranteeing the ethics and quality of our work.” All Metalor’s production sites are certified to ISO 9001, which covers quality management. The group was also the first refiner to obtain an ISO 17034 certification, which authorises it to produce reference metals for quality control.
The company continues to collect certifications – it has 29 to date. An entire department is dedicated to monitoring them.
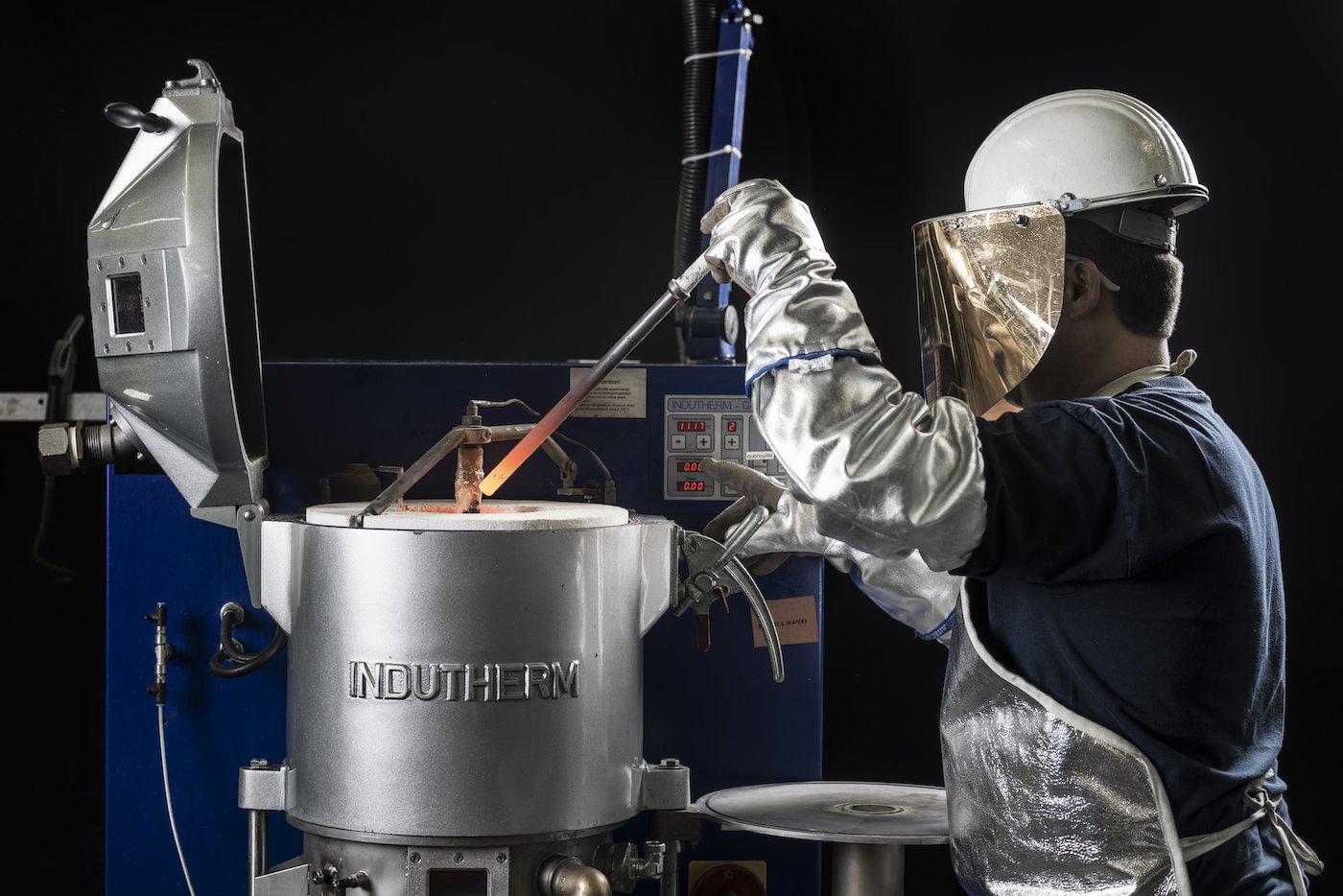
A photovoltaic experiment in Mexico
Antoine de Montmollin sums up his approach: “Our business is based on knowing our customers and suppliers. Performing our due diligence in depth is essential. Only 50% of the world’s gold production has guaranteed provenance. We therefore restrict ourselves to this identifiable part and refuse to source gold beyond this. We have to be as transparent as possible.”
For the past two years, Metalor has published a comprehensive CSR report disclosing targets, whether met or missed. The group has three fundamental pillars: transparency and responsible sourcing, social responsibility and environmental impact.
Manufacturing uses a lot of electricity, which is a major source of CO2 emissions. Metalor wants to reduce its electricity use from 45,695 MWh in 2021 to 38,389 MWh in 2030, i.e. by 16%. To achieve this goal, the company plans to deploy photovoltaic parks at 9 of its 14 production sites. A successful experiment in Mexico in 2021 (a site that today is almost 80% photovoltaic) has convinced the company of the merits of this approach, for which a budget of CHF 12 million has been made available.
As the head of Metalor for three years, Antoine de Montmollin has opted for dialogue with stakeholders: suppliers, customers, NGOs and the press. In a world where secrecy is the rule, this strategy is unusual.
“The decision was taken very quickly by Tanaka [the Japanese owner of Metalor],” explains de Montmollin. “They understand what is at stake and support the investments. Family governance is an accelerator in this context.” The group has already seen its carbon emissions reduced by 30% between 2018 and 2021, down from 22,552 tonnes to 15,552 tonnes, even as its turnover increased by 27%. The current objective is to continue to reduce emissions by 11% per year until 2030.
This objective also encompasses improvements in heat recovery, cooling system efficiency and the reduction of water consumption. “We are also looking at how to improve the efficiency of our furnaces around the world and minimise the impact of transport on our operations,” adds the CEO.
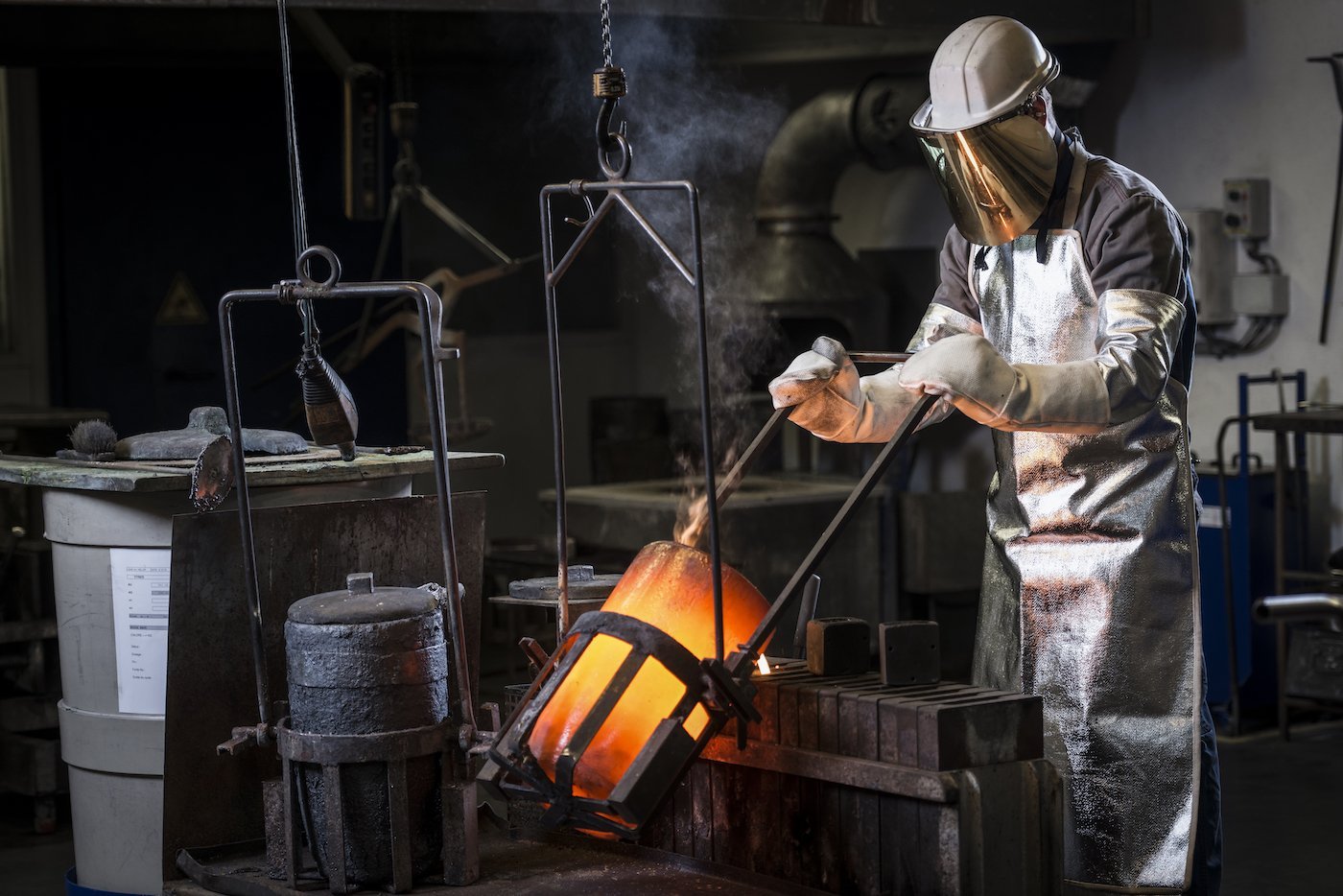
A passport to trace gold
Improving traceability is a top priority for Metalor, which is investing in innovative solutions. In 2019, it developed the Geoforensic Passport for its mining activity – a scientific validation of the “DNA” of the gold that identifies the exact mine from where it was extracted. This small revolution aims to avoid grey flows of gold from countries in conflict, or from mines known for their harsh working conditions or links with drug money laundering (such as the Rinconada mine in the Peruvian Andes, the highest mine in the world).
Pessimistic observers will see this as an a posteriori certification; the more optimistic as an unfalsifiable guarantee of origin. The tool is clearly useful, especially as Metalor has decided to open up the passport to anyone who wishes to use it. The authorities concerned were quick to recognise its value: Brazil and Tanzania saw it as a means to help combat illegal practices that are dangerous for indigenous populations and harmful to the environment.
“This will not necessarily prevent illegal exploitation of these places, but it will make it much more difficult for them to distribute their gold and therefore potentially, in the long term, render them unprofitable to operate,” notes Antoine de Montmollin.
Recycled gold accounts for almost 64% by volume of the material refined at Metalor. Its “traceability is more complex,” concedes Antoine de Montmollin.
Beyond the supervision of gold extraction, what happens when it arrives on site? How is it identified? “Each batch is treated separately, for one obvious reason: we first have to sample and evaluate each batch so that we can settle the invoice with the supplier before refining them to 999.9‰,” Metalor’s CEO replies.
What about recycled gold, which accounts for almost 64% by volume of the material refined at Metalor (as well as 87% of silver, 99.83% of platinum and 99.84% of palladium)? “It’s more complex,” concedes de Montmollin. “Recycled gold comes from various sectors, such as medical, aeronautics, electronics and scrap jewellery, but it is impossible to know where it was mined. Once it is out of the ground and into the system, it is unclear. Its impact in terms of CO2 emissions is obviously very low compared to mining, but for traceability we have to rely on standards like the RJC Codes of Practices and Codes of Conduct. And we segregate the sources that we are totally sure of. All this information is then integrated into our Metalor Check app, which enables us to identify Metalor gold (bars, ingots, etc.). We’re working to put in place a complete ecosystem.”
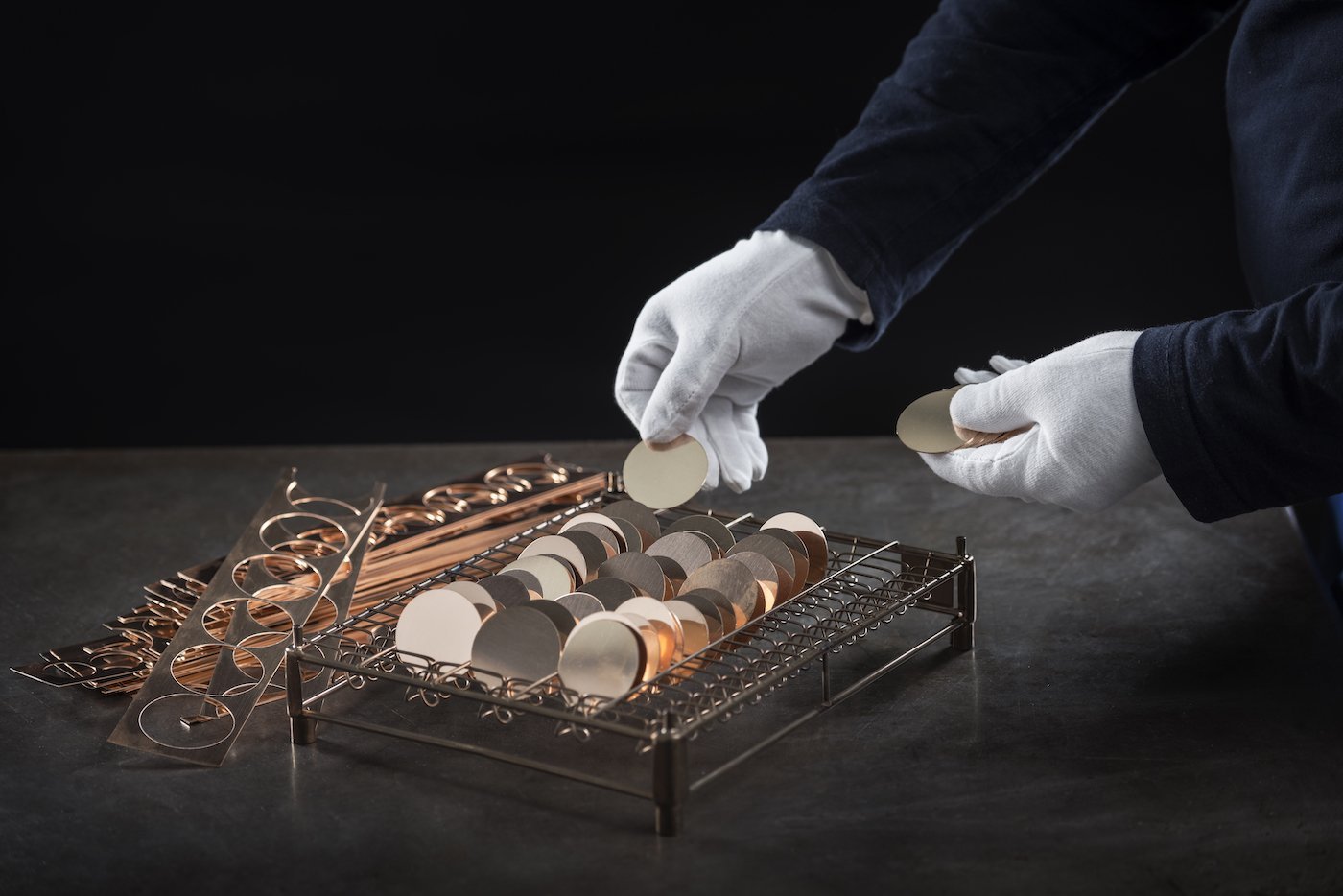
Watchmaking roots
To understand the path taken by Metalor, let’s take a look at its history. It all began in 1852, in Le Locle, with the foundation of Martin de Pury & Cie, which melted down the gold used to manufacture pocket-watch cases. The company’s structure evolved over time; it was first bought by the Banque du Locle in 1864, then by the Société de Banque Suisse in 1918. In 1998 it was taken over by a group of private investors led by Ernst Thomke and became independent.
-
- The factory floor of Métaux Précieux SA, an ancestor of Metalor
The name Metalor Technologies was introduced in 2001. The company was resold to a private equity group, Astorg Partners, in 2009. The latest change came in 2016 when the Japanese group Tanaka Kikinzoku, established in 1885, took over. Like Metalor, the Japanese company is one of the biggest players in the precious metals sector and one of the five referees of the London Bullion Market Association (LBMA) and the London Platinum and Palladium Market (LPPM). This purchase positioned the company to pursue global industrial objectives.
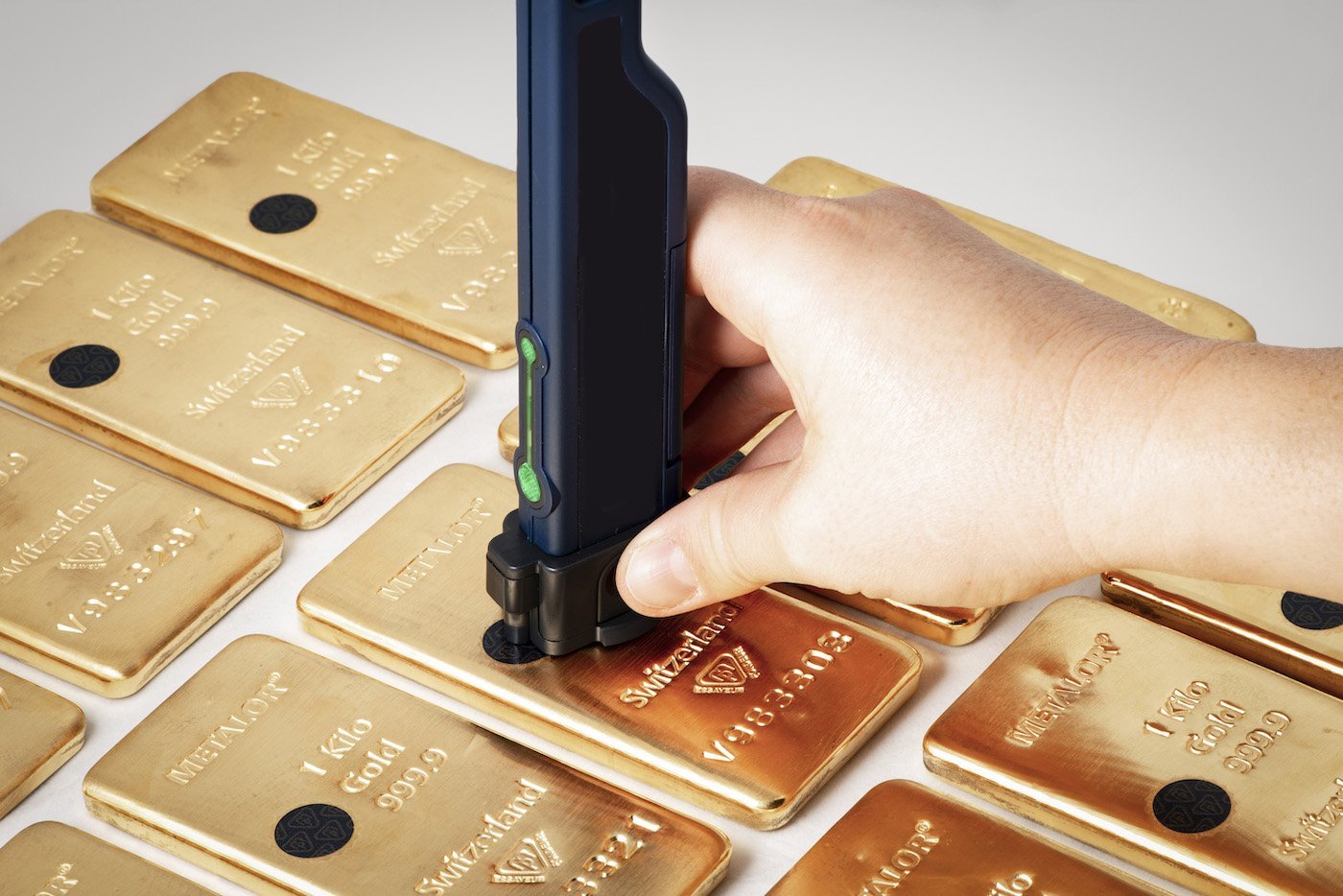
The dilemma of artisanal mines
Clear governance allows difficult decisions to be made more quickly. For example, when Antoine de Montmollin wanted to stop sourcing from artisanal mines (known as ASM – Artisanal and Small-scale Mining) at the end of 2019, at the risk of being accused of abandoning the local populations that depend on them (nearly 100 million people), the decision was made in a matter of days.
“This is the price we had to pay to ensure transparency, which is essential for our business,” explains the CEO. “We were no longer able to guarantee the real origin of the ASM gold, nor the quality of the extraction methods, nor the working conditions. This created a small earthquake in our discreet world. We have withdrawn from ASM with regret, as we are well aware of the need to support the millions of people who depend on it. But our primary desire is to guarantee traceability.”
The door is not completely closed to collaboration with artisanal mines, de Montmollin stresses: “We are still open to projects put forward by potential partners and we have already re-committed to two projects.”
The first of these projects is the refining of gold from the Peruvian mine of Yanaquihua, whose gold Metalor has been refining since 2020 in partnership with Swiss Better Gold and the Swiss State Secretariat for Economic Affairs (SECO).
The second is a philanthropic project which has seen the refiner partner with the Alliance for Responsible Mining NGO. This project finances part of the Fairmined certification process for an artisanal mine in Colombia. The aim is to accompany this type of mine towards certification in order to guarantee the production of ethical ASM gold and increase gold miners’ awareness of environmental concerns.
“We were no longer able to guarantee the real origin of the ASM gold, nor the quality of the extraction methods, nor the working conditions.”
For Antoine de Montmollin, the change of ownership has proved beneficial to the steps initiated by his company: “Being part of a family group like Tanaka allows for quick action. Decisions such as getting out of ASM, investing 12 million francs in photovoltaics or financing a mine in Colombia to secure Fairmined certification – without using the gold afterwards – would not have been possible elsewhere. Philanthropy, or any decision where the return on investment is not immediate, are foreign concepts to large investor groups.”
As the head of Metalor for three years, Antoine de Montmollin has opted for dialogue with stakeholders: suppliers, customers, NGOs and the press. In a world where secrecy is the rule, this strategy is unusual. “We want to be transparent at all levels,” he explains. “We want to show that we have nothing to hide. Our CSR report is part of this logic. We are aware that there is still a long way to go, but we believe that talking openly about it helps to spread best practices.”
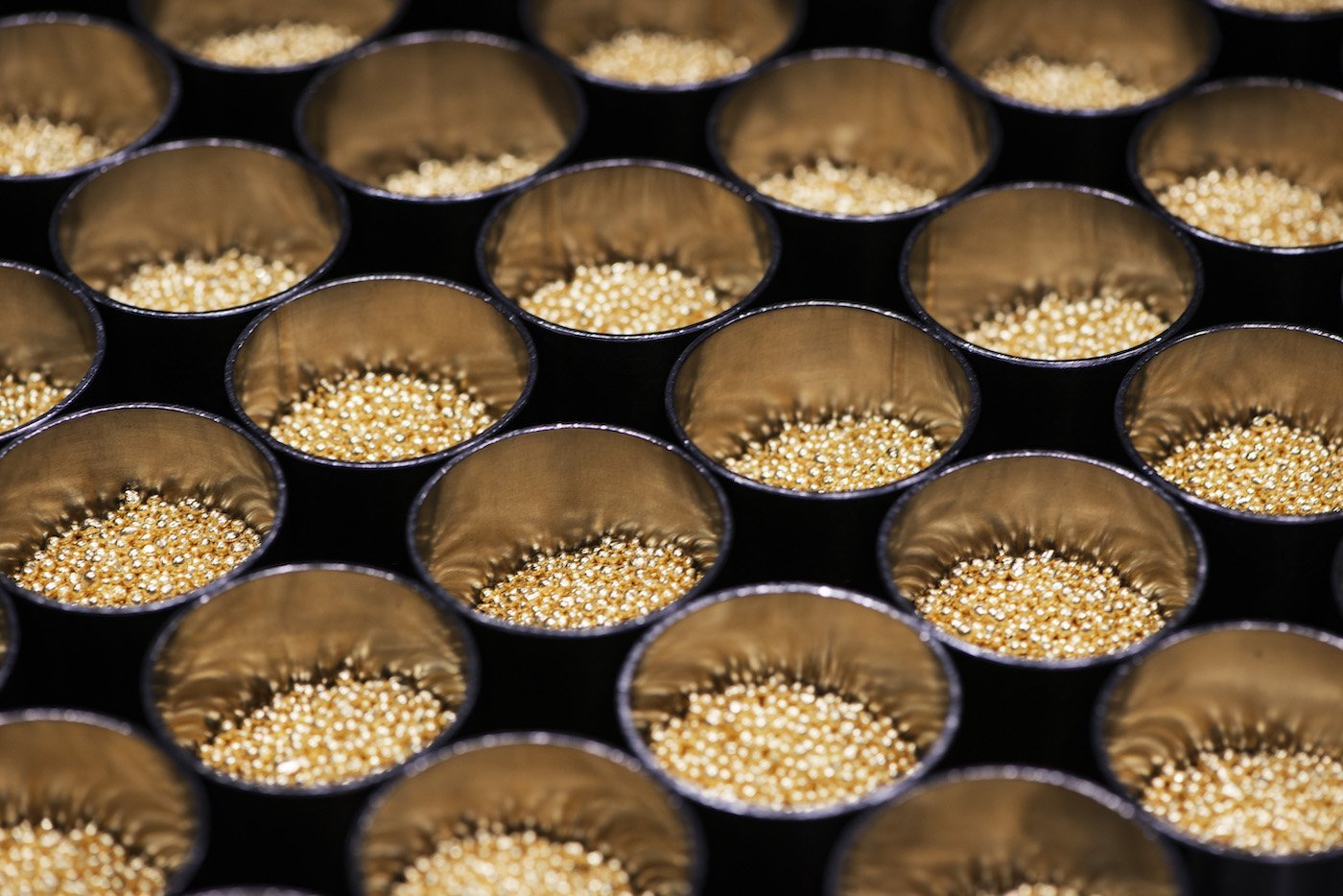
Local or global circuits?
Metalor’s business has grown strongly around the world since the 1960s, with the opening of multiple sites – first in France (1963), then in the USA and Mexico (1989 and 1997), in China in Suzhou (2003 and 2014) and Hong Kong (2007), and finally in Japan, South Korea (2011) and Singapore (2013).
Wouldn’t opening facilities on multiple continents run counter to reducing Metalor’s carbon footprint? “Not at all,” replies de Montmollin. “On the contrary, these factories have been set up in the regions where their output is used. We avoid intercontinental transport and its major impact.”
What about the chemical treatments used for production? “That remains one of the areas for improvement,” the manager says. “We are working on solutions other than chlorine, such as the use of hydrogen peroxide. On the other hand, as our chemicals are mainly inorganic acids and bases, we carry out acid-base neutralisation operations in our wastewater treatment plant. This process allows us, after carrying out daily analyses as per the Water Protection Ordinance (OEaux), to transfer the effluent to the municipal wastewater treatment plant under the supervision of the energy and environmental authorities. In other specific cases, our chemical residues are treated as special waste by an authorised and certified partner.”
There are many parameters that are driving change. Any environmental, social and governance (ESG) approach is ultimately linked to the company’s own governance and long-term vision. In this respect, Metalor is demonstrating a transparent approach, on its own initiative, at the urging of the general public, and at the behest of end users who are themselves under increasing pressure to bring about change, in the watch industry as elsewhere.